Stainless Steel Technical Guide
Class II – Ferritic Stainless Steels
Some of the common ferritic stainless steels are shown in Figure 10. Note that the AISI 400 series covers the ferritic as well as the martensitic stainless steels. As Cr content is increased beyond the 11.5-18% range of the martensitic class, the predominant metallurgical structure is ferrite, even at elevated temperatures. See Figure 11. In some grades, there is enough C and nitrogen (N) to result in some austenite at high temperatures and hence, partial hardening on rapid cooling. However, generally speaking, the ferritic stainless steels are relatively non-hardening.
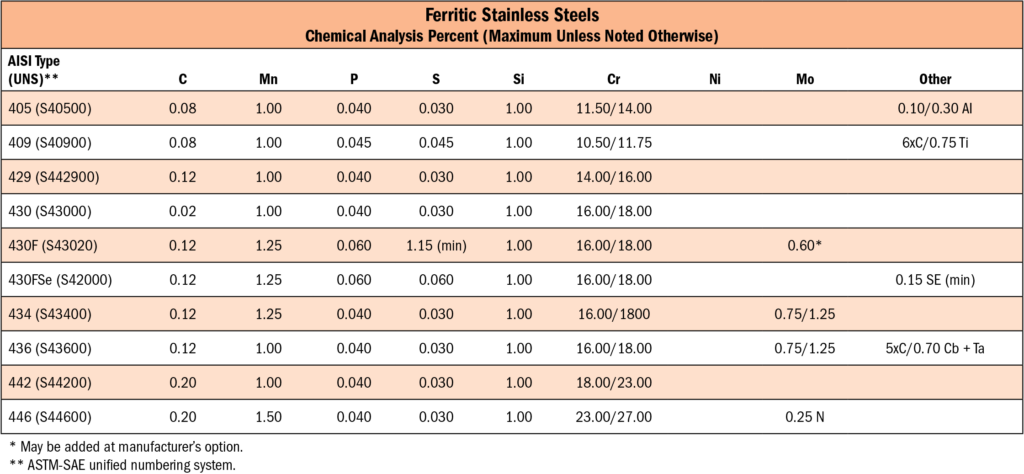
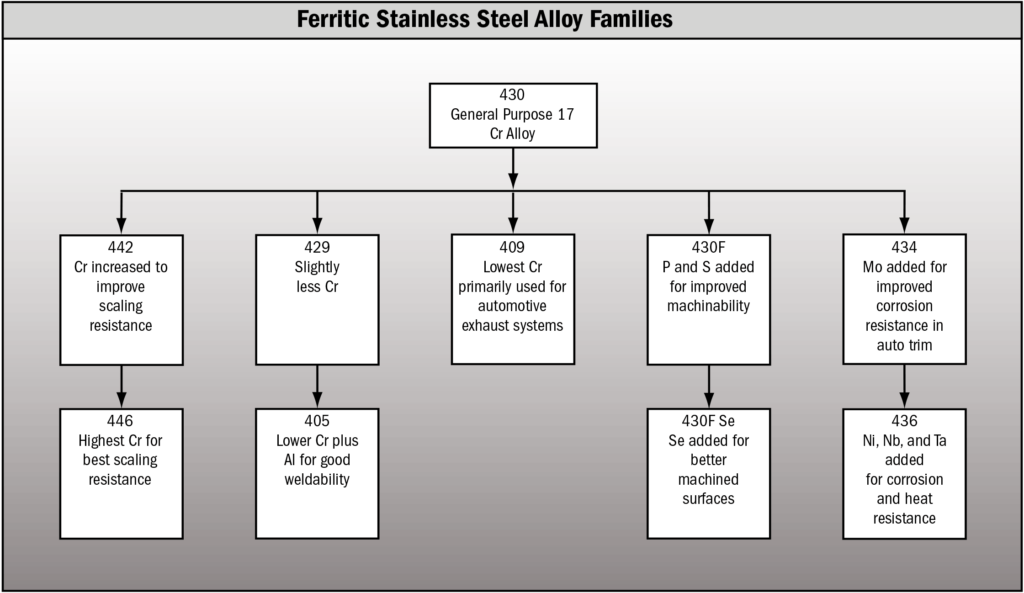
The martensitic class of stainless steels shown in Figure 7 depend primarily on Cr from 11.5 to 18% as the major alloying element. This class and the ferritic stainless steel class share the AISI 400 numbering series. They are sometimes referred to as straight chromium grades. In contrast, the austenitic stainless steels are essentially chromium- nickel alloys; they are covered by the AISI 300 series for most standard compositions of wrought products. AISI 410, the principal alloy of the martensitic class, ranges 11.5 to 13.5% Cr. However, the relatively new 13Cr / 4.5Ni / .5Mo low carbon casting grade CA-6NM, provides higher strength, increased toughness, better weldability and greater corrosion resistance than the CA-15 (Type 410) casting grade.
Martensitic stainless steels exhibit magnetic properties similar to those of plain carbon steels and, therefore, are also subject to arc blow in welding. Unlike mild steels, they are air-hardening when allowed to cool rapidly from the austenitizing temperature range (1600-1850°F) where the austenite phase is predominant.
Austenitizing temperatures are reached in the heat-affected zones of weldments and subsequent cooling occurs at rates sufficient to produce martensite. In the annealed condition martensitic stainless steels have basically a ferritic microstructure with dispersed chromium carbides (See Figure 5 and Figure 6).
Carbon and chromium in the martensitic stainless steels act in concert to prevent transformation of austenite to ferrite during rapid cooling. The result is the distorted BCT structure called martensite (body- centered tetragonal — like BCC but elongated in one direction). The heat- affected zone on either side of a weldment will develop the hard, brittle martensite phase and, unless local preheating is practiced, may develop cracks due to shrinkage stresses and hydrogen. The hardness of the heat-affected zone depends primarily on the carbon content of the base metal. Increased hardness results in decreased toughness and more susceptibility to cracking. Although the most suitable preheat and interpass temperature will depend on carbon content, the mass of the joint, degree of restraint and the filler metal composition, temperatures of 400-600°F are commonly specified.
From the foregoing, it is obvious that prolonged heating of ferritic stainless steels within the 700-1700°F range should be avoided. Welding heat input should be minimized and slow cooling from welding avoided. Despite this, preheating of 300-450°F is recommended for welding when thickness exceeds about 1/4”, since ductility of the base metal is improved in that temperature range — particularly in the heat- affected zone which may contain some martensite.
Postweld heating of the low chromium ferritic stainless steels at 1450 to 1550°F will assure a wholly ferritic structure and partially restore mechanical properties and corrosion resistance that may have been adversely affected by the welding temperatures. However, exposure within this temperature range will quickly produce embrittling sigma phase in the higher chromium alloys such as 444 or 26-1. To minimize distortion, cooling may be done in the furnace down to no lower than 1100°F but prolonged exposure in the 1050-750°F range should be avoided due to 885°F brittleness.
Because of embrittlement problems, the ferritic stainless steels are not considered readily weldable and are used primarily for nonstructural applications. They are recommended for resistance to chloride stress- corrosion cracking, corrosion in aqueous media, oxidation at high temperature and pitting and crevice corrosion in chloride media. Applications include automobile exhaust equipment, radiator tanks, catalytic reactors, culverts, dry fertilizer tanks and animal containment housings. Type 430 is used for decorative trim, nitric acid tanks and annealing baskets. Type 442 is used for components requiring protection from scaling at high temperatures such as furnace parts, nozzles and combustion chambers.
Matching metals for most ferritic stainless steels are not readily available. The 409 and 439 are available from some manufacturers as a tubular metal cored product. They are primarily used in automotive exhaust welding applications. Austenitic filler metals such as 309, 310 and 312 are often used where the application can reconcile the different corrosion-resistant characteristics and the greater coefficients of linear expansion of the austenitic grades. Where postweld annealing at 1450°F is specified, the austenitic filler metal should be either a stabilized or low carbon grade to avoid carbide precipitation. See page 14 for discussion on carbide precipitation.
Solid wires for GMAW or GTAW are available in 410 and 430 compositions.

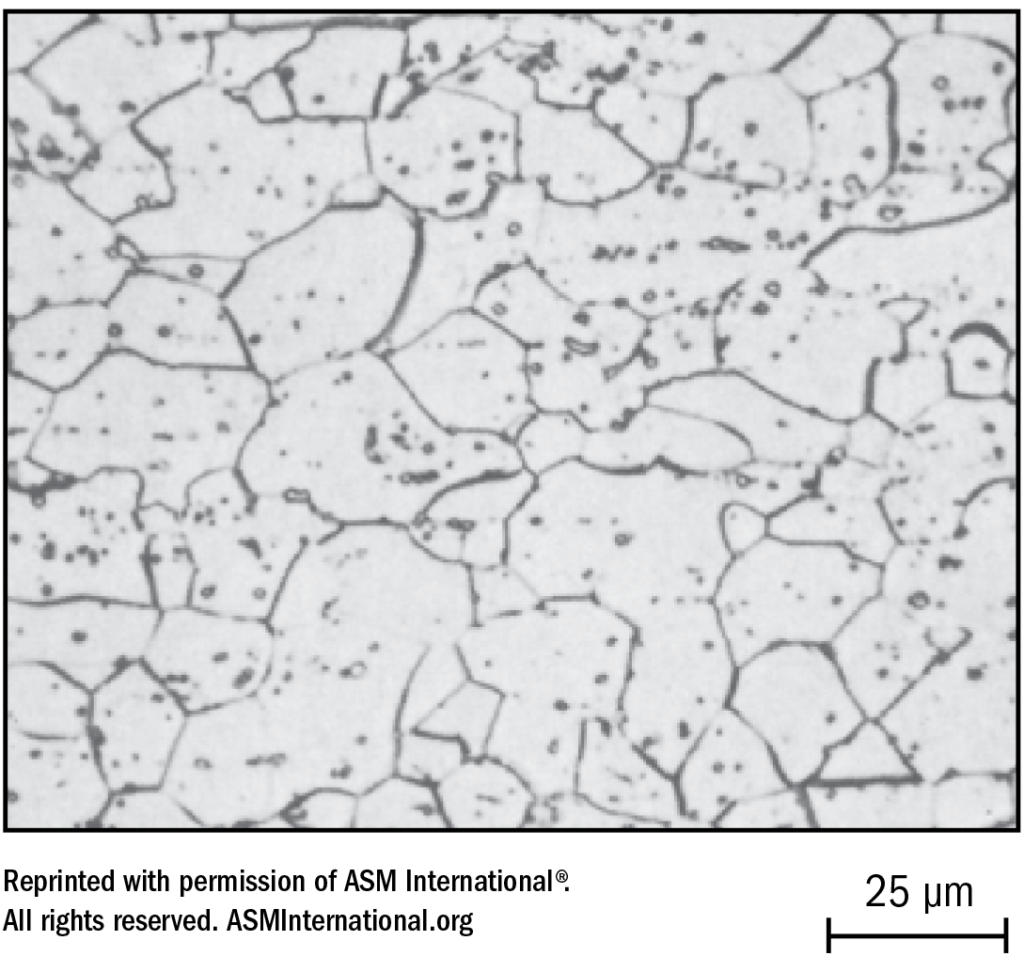