Marine & Shipbuilding
Commercial or Military. Marine Projects Depend on Welders. Welders Depend on Hobart® Filler Metals.
Durability. Strength. The right filler metal makes all the difference. From large shipyards to recreational boat fabrication, maximize your welding process and efficiency savings. To ensure you meet your customer’s needs, you need filler metals that you can count on: Hobart® filler metals.
Choosing the wrong filler metal can leave you dead in the water.
Weldability is key to shipbuilding, so make sure you have the right material for your projects. Find the best Hobart filler metals from our inventory of materials for every application. We’ll work together to ensure you have the filler metals to deliver the quality your customer expects, just like we did for Marine Group Boat Works.
It’s the tie that binds DURABILITY + STRENGTH
Marine Group Boat Works relies on the strongest filler metals to build U.S. Navy Dive Boats. See why they trust Hobart filler metals to meet demand-critical requirements of dive boats for the U.S. Navy.
Products
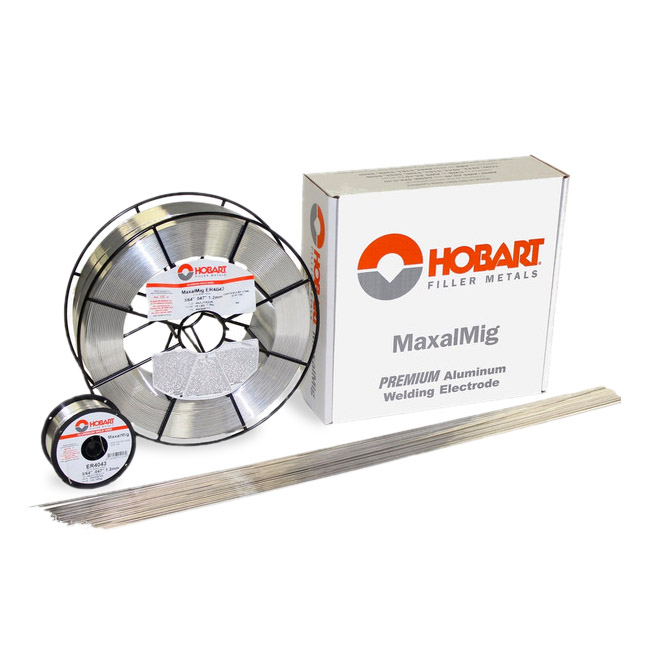
Hobart® MaxalMig® 4943
AWS: A5.10: ER4943, R4943
Alloy 4943 filler metal was formulated to be welded with the same weld procedure specifications as 4043 and 4643, and does not depend upon dilution from the base metal during welding to increase the strength of the weld deposit, while maintaining the same weld characteristics and benefits of 4043 and 4643. Features/Benefits: – 25% higher UTS & 50% higher yield strength than 4043 in the as welded condition (typical) – Moderate/high strength (35 ksi typical) – Low melting temperature/high fluidity – Low welding smut and discoloration – Low ductility, formability, and lower toughness (similar to 4043) – Moderate electrical conductivity and thermal conductivity – Post weld fully heat treatable requiring no base metal dilution – Excellent corrosion resistance – Low shrinkage rate/reduced distortion – Low hot cracking sensitivity in most applications
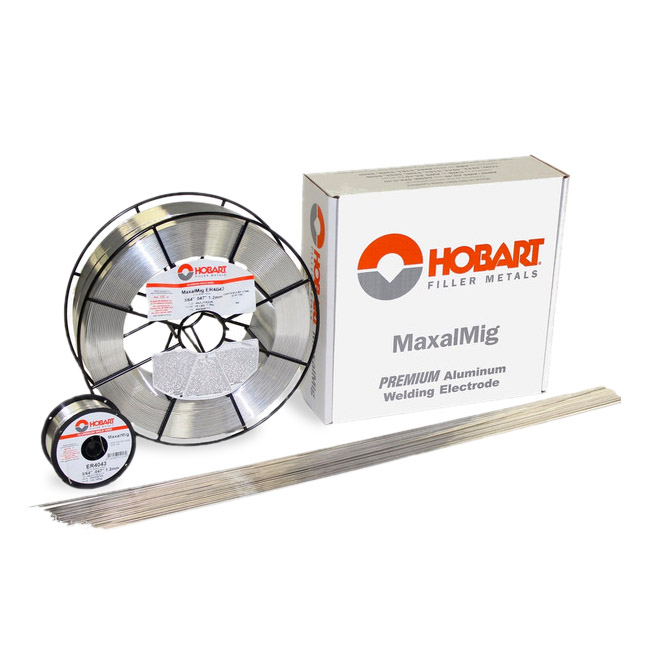
Hobart® MaxalMig® 5356
AWS: A5.10: ER5356, R5356
5356 filler metal is the most common aluminum/magnesium alloy for general purpose welding and is typically used in the construction industry in fabricating truck trailers, small fishing boats, and in cryogenic applications. Features/Benefits: – High strength (38 ksi typical) – High ductility/fatigue strength/very high toughness – Moderate ductility/formability – Lower electrical conductivity and thermal conductivity – Higher column strength/better feedability – Very good color match after anodizing with 5xxx/6xxx base materials
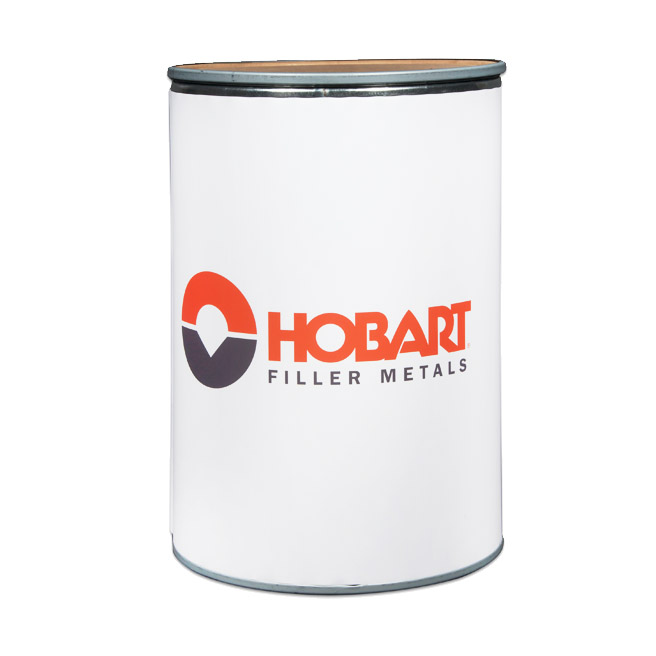
FabCO® Triple 7
AWS: A5.20: E71T-1C/M H8, E71T-9C/M H8 A5.29: E81T1-GC/-GM H8
Intended for single and multiple pass applications in all positions. Designed for carbon and higher strength steels.
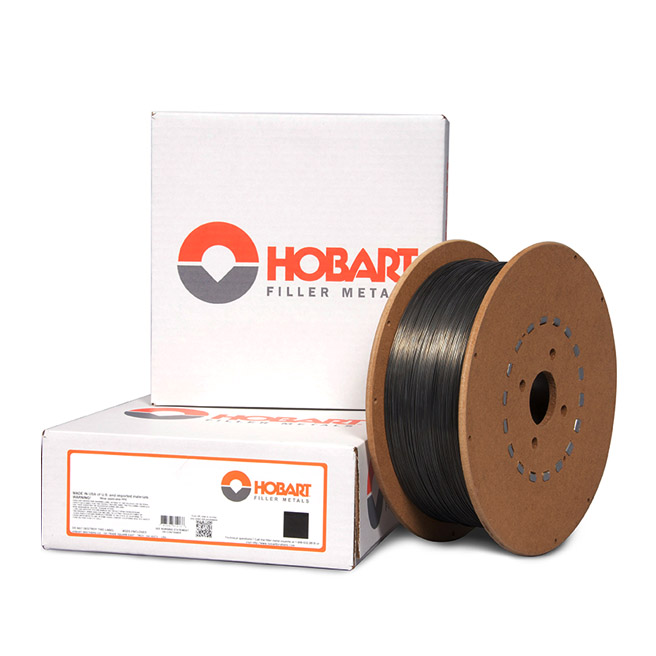
FabCO® Excel-Arc™ 71
AWS: A5.20: E71T-1C/M H8, E71T-9C/M H8
All position wire for both CO2 and mixed gas. For mild and low alloy steel applications.
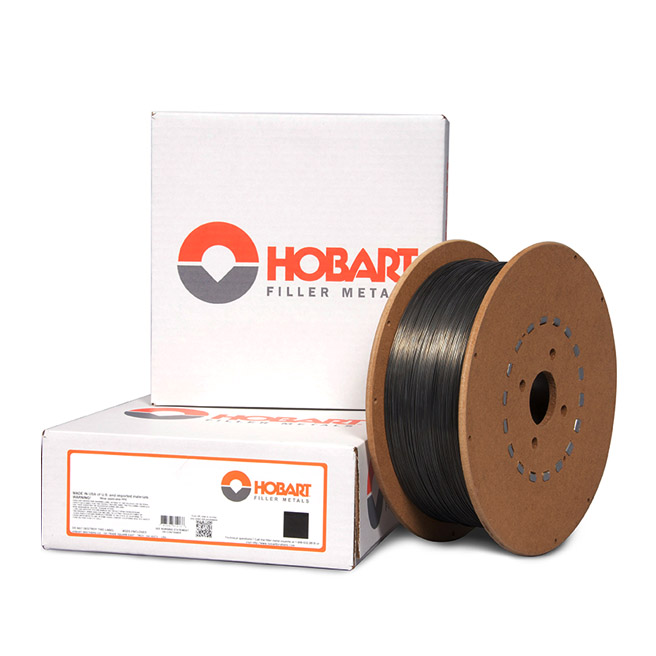
FabCO® Element™ 81K2C
AWS: A5.29: E81T1-GC H8
Designed as a low Manganese (Mn) replacement for E81T1-K2C products. Meets all requirements of E81T1-K2C classification except for the minimum Mn requirement. This product offers reductions of Mn in the weld fume of 60-80% over a standard E81T1-K2C with low diffusible hydrogen as well as enhanced operator appeal and excellent out of positional capability.
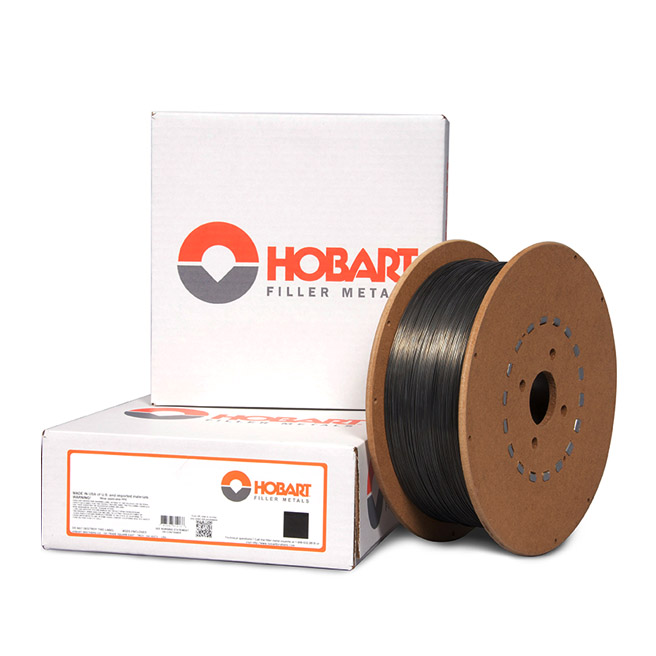
FabCO® Element™ 81K2M
AWS: A5.29: E81T1-GM H8
Designed as a low Manganese (Mn) replacement for E81T1-K2M products. Meets all requirements of E81T1-K2M classification except for the minimum Mn requirement. This product offers reductions of Mn in the weld fume of 60-80% over a standard E81T1-K2M with low diffusible hydrogen as well as enhanced operator appeal and excellent out of positional capability.
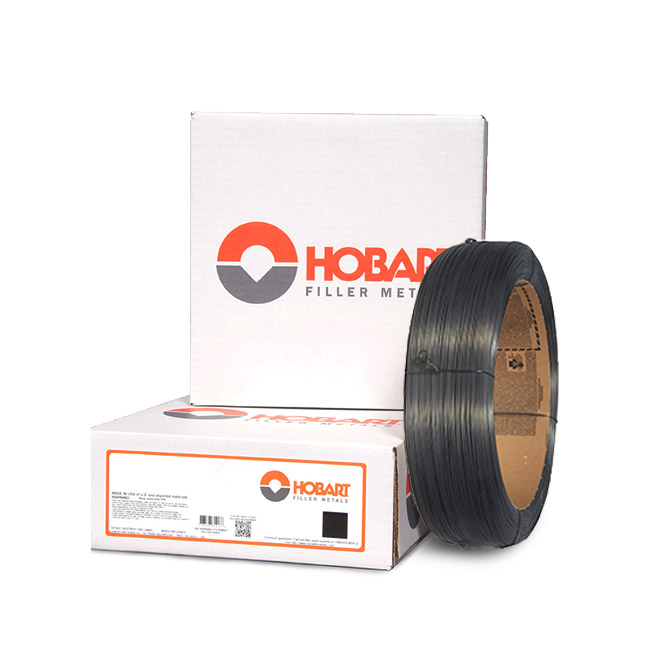
SubCOR™ EM13K-S MOD
AWS: A5.17: EC1
SubCOR EM13K-S MOD is a composite electrode for submerged arc welding of carbon steel plates using the recommended fluxes. This wire is specially formulated to maintain good mechanical properties when welding at high heat inputs. The electrode chemistry conforms to the solid wire classification EM13K per AWS A5.17.
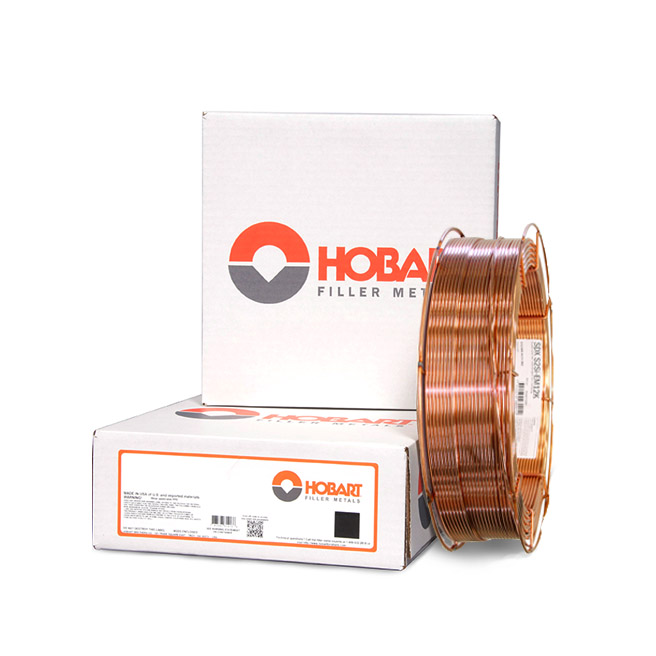
SDX S2Si-EM12K
AWS: A5.17: EM12K
SDX S2Si-EM12K is a copper-coated carbon-steel solid wire for submerged arc welding. SDX S2Si-EM12K is a versatile, general purpose product suitable for joining a wide range of non-alloyed steels with a wide variety of flux(es). ** In an effort to best serve the packaging needs and requirements of our customers globally, this product features region-exclusive part numbers. To obtain the complete list of part numbers available in your region, e-mail us at subarc@itw-welding.com, contact your regional ITW Welding office, or contact Hobart Brothers customer service (North America) **