Today’s Welder Training: A Look at Tulsa Welding School
According to the American Welding Society (AWS), the U.S. is poised to reach a deficit of 300,000 welders by 2026 as baby boomers enter retirement and fewer younger welders join the profession. This shortage could have far-reaching consequences for many industries — drops in production, the inability to meet customer demands and lost revenue, to name a few. With new infrastructure plans and goals, construction and clean energy initiatives in particular stand to feel a significant impact.
At Tulsa Welding School in Tulsa, Oklahoma, instructors designed the Professional Welder program to help prepare students with the skills needed to successfully enter the workforce. Recruitment efforts also encourage entry into this trade, sharing the rewards of building a career in welding with potential students.

“Based on our curriculum at Tulsa Welding School, everything that students learn as they go through the program is going to translate into a real-world aspect,” said Chris Schuler, director of training and student services. “The majority of the welding positions they learn are going to be on the weld test they’re going to take to gain employment.”
According to Schuler, that knowledge and skill gives graduates a leg up on the competition. When they show up for an interview and secure a job, they need very minimal training, if any. Employers simply need to review customer preferences with their new hires, which gives the company a fast track to get work done and makes it easier for the students to adapt as new employees.
Setting the foundation for success
In the 10 years Schuler has taught at Tulsa Welding School, he’s seen a wide array of students entering the program. Many times, students have been in an agriculture program in high school or have participated in Skills USA, where they pick up welding skills. But more and more, there are students of all ages who have never even touched welding equipment and are looking at the opportunities in the industry as a first career or after numerous careers. They see that welding is lucrative and in demand. And an increasing number of women are entering the program.
Regardless of age or gender, however, there are some key factors that Schuler says welding students need to consider to set themselves up for success. He sees these as integral to students entering any welding program, not just at Tulsa Welding School.
Attendance is 100% the main requirement.
Schuler said, “We’d rather have an average welder with perfect attendance versus a perfect welder with average attendance — because if they show up, we can help them to learn even more. We’ll teach them what they need to know.”
Along with that, keeping an open mind is important. The instructors recognize that students might be nervous, but encourage them to be prepared to ask questions and to listen. This can help new employees in the workplace, too, when they are asked to learn the company’s way of doing things.
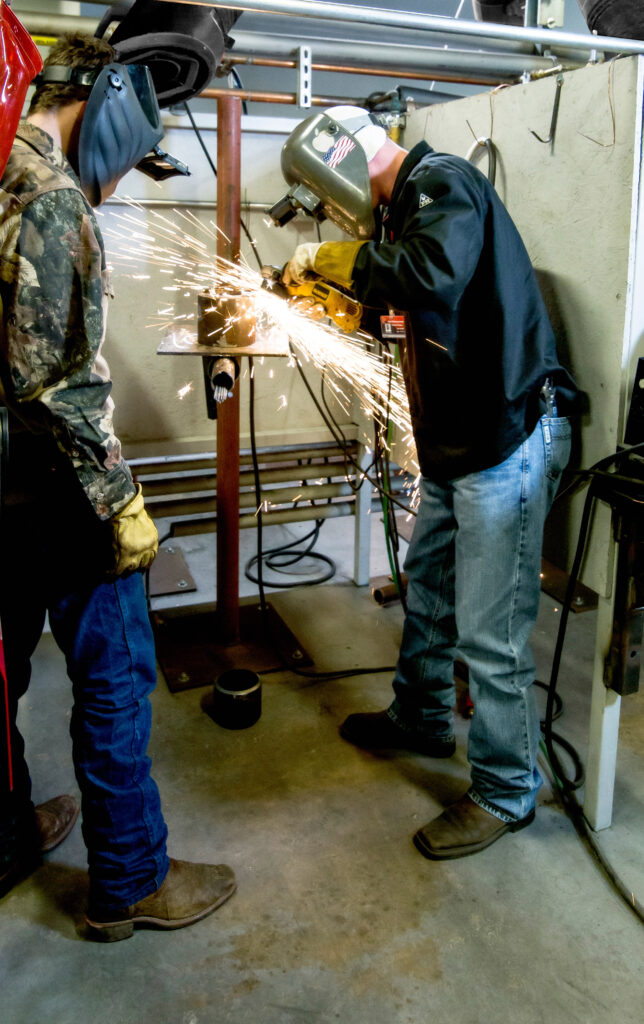
“Our instructors have been hit with every question under the sun. They’re prepared for the questions, and students need to take advantage of that,” explained Schuler. “Our instructors come from the field, so they’ve been in every area of the industry these students want to go work in.”
Schuler and the other instructors meet with local employers twice a year to find out what students should be learning to join their company and build a viable career. Employer feedback not only helps inform the program’s curriculum and keep it current, but it also provides insight into soft skills that can help them succeed. According to these employers, having a positive attitude and being able to communicate clearly are both valuable traits they seek in potential hires.
Building a solid relationship between the instructors and students also contributes to the students’ success. Schuler says he wants students to keep an eye on the instructor who’s been where they want to be. The students can then have a mentor and a role model to help them understand what to expect when they get out on the job.
“I think it’s definitely important to have an understanding between the two of why they’re each here. The instructor is here to help the student. The student is here to learn,” explained Schuler. “We’re training them to be professionals, so we have to have the answers they need.”
Student Gena Langley appreciates that about the program.
“I only have positive things to say about my instructors and my experience here. Everyone is super willing to help. I have never felt afraid to ask any questions,” she said. “I had never welded before in my life, but I don’t think that I was treated any differently than somebody who already had an idea of what to do.”
Must-knows for welder training
The Tulsa Welding School philosophy is to provide students with a well-rounded curriculum that builds not only their hands-on skills but also their general knowledge of welding. That includes proper terminology that will set them up for successful communication with future employers and coworkers.
The first course in the Professional Welder program focuses on welding fundamentals to help build critical skills, inform students of career opportunities and teach them safety best practices. These, along with learning to read construction drawings and weld symbols, are must-haves in the students’ education. In this course, they also learn how to set up welding equipment from Miller Electric Mfg. LLC and begin shielded metal arc welding (SMAW) with AWS E7018 electrodes from Hobart, along with learning plasma cutting and carbon arc gouging.
The remaining five welding courses in the program include Gas Metal Arc Welding (GMAW)/Flux-Cored arc welding (FCAW), Structural Welding, Pipe Welding, Advanced Pipe Welding and a Welding Capstone course. This final course is designed to help the students transition from the classroom to the field by focusing on projects that test their welding knowledge and hone their skills. They also are challenged to meet production rates that are at industry standards.
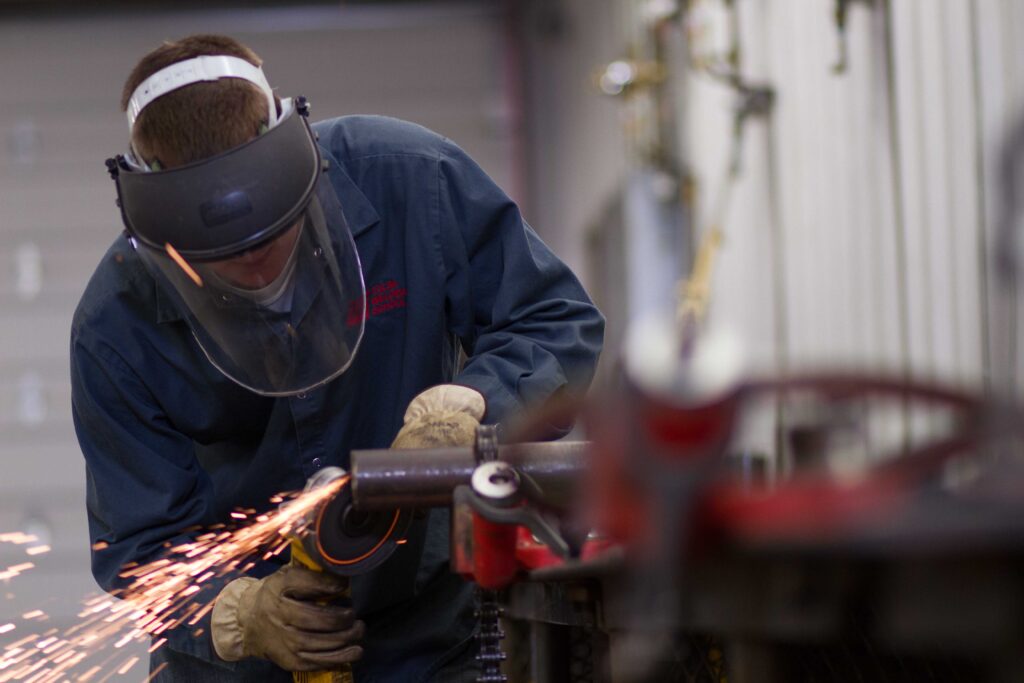
Besides the hands-on training, there’s even more to the program for Langley.
“For me, once I get here and I get all my PPE on and everything, I’m in the zone. Anything that may be troubling me in regular day-to-day life just goes away. It’s like meditation. And I love it and I love that everyone has been super helpful and encouraging.”
Entering the workforce
For Tulsa Welding School students who want to go to work for a specific employer, instructors can help them reach that goal. They provide additional training to meet that employer’s customer recommendations. This also helps support local companies in their recruitment efforts. Graduates enter a variety of fields — everything from welding structural buildings and cell phone towers to building government-contracted submarine parts.
“A lot of the employers we deal with come to us and ask for candidates,” said Schuler. “We screen the students, making sure they’ve had good attendance and have done well in the program. We put them in front of the employer, and oftentimes they will come in and administer the weld test here on campus.”
In addition to offering training to meet company expectations, instructors encourage students to hone their skills in every process — even if they aren’t particularly interested in it.
“We have students that may not care for a process and say that they are never going to run it,” Schuler shared. “We let them know that they need to learn everything because the demand for people right now in the industry is so broad, and they’re all doing different things. The goal is to make themselves more marketable. In the end, that helps both them and the industry’s demand for new welders.”
Republished from Welding Journal (April 2023) with permission from the American Welding Society (AWS). Click here to view the original article.