Tips for Maximizing Productivity and Decreasing Costs in Job Shops
The goal of any job is to complete it correctly, on time, within budget and with the greatest amount of efficiency — and it’s no different for welding applications in a job shop. Improving productivity, ensuring the best quality and reducing costs are all important if job shops are to remain competitive and provide the best, and most timely, service and products to their customers.
There is more to keeping to these goals, however, than just having the fastest employees or a particular piece of equipment. Factors like product storage (particularly filler metals), welding operator safety and training, and effective purchasing are also critical. As job shops become more sophisticated, it’s also important to find the most efficient ways of managing the quality- and productivity-enhancing aspects of the welding process.
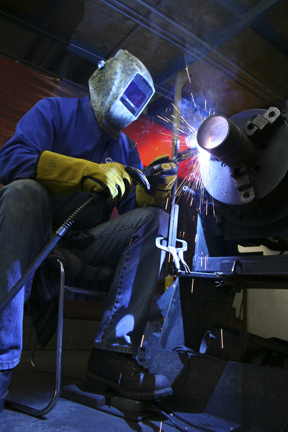
quality and reducing costs are all important
if job shops are to remain competitive and
provide the best, and most timely, service
and products to their
customers.
Here are five key tips to help job shops meet their goals — all while gaining that competitive edge.
Offer ongoing educational opportunities and training to employees
Investing time and money into training can yield significant long-term benefits for a job shop. Welding operators benefit individually from process and equipment training, and in many cases, it can also help them optimize the welding operation for greater efficiency. Proper training also can give job shops a competitive edge over those that have less-skilled labor, and it promotes teamwork among employees.
Training opportunities typically are available through equipment and filler metal manufacturers or welding distributors. In some cases, working with a local technical college can offer training for specific applications.
Employee involvement and training is based on the idea of continuous improvement. Better-trained welder operators are more involved in the process and more invested in the job they do. It empowers employees to have ownership of their portion of the process.
Proper training takes a commitment of time and effort, but the investment can pay off in the long run by reducing downtime, inefficiencies and lost productivity, and by improving quality of the end product.
Instill proper safety measures
Addressing the weld fumes created by welding processes is one way to create a cleaner, more productive job shop. Along with making employee comfort a priority, controlling weld fumes also helps ensure compliance with regulations.
There are many options for weld fume management, and selecting the best solution depends on cost, space and the actual welding applications conducted in a job shop. Also, note that every welding environment is different and should be inspected by a qualified industrial hygienist to determine the appropriate course of action for fume controls.
Modifying the welding process can help reduce weld fume. Changing base material, wire, gas, process, and/or optimizing parameters are all options job shops can utilize. Teaching employees proper weld positioning to minimize exposure to the weld fume path is also important. Welder operators should not position themselves directly above the weld and should never stand between a fan and the weld.
Beyond welding process and behavioral changes, the next step is to consider engineering controls such as source capture systems. Source capture is designed to draw weld fume away from the welding operator’s breathing zone and keep the facility cleaner. These systems, however, can be difficult to position over large weldments or obstructions in the weld cell.
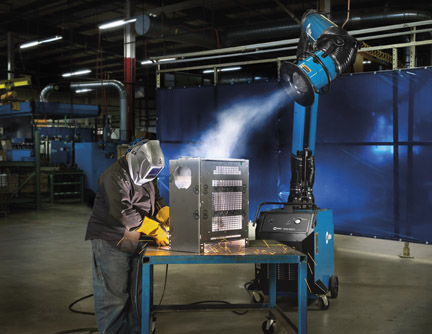
is one way to create a safer, more productive job shop.
Along with making employee comfort a priority, controlling
weld fumes also helps ensure compliance with regulations.
New advancements in source capture technology are making that challenge easier. These mobile fume extraction systems increase the fume extraction area to a greater width and distance — up to 4 feet wide and 5 feet away. This larger capture area reduces downtime and pauses during welding that are spent repositioning the capture arm. This extended capture system is the best choice for any weldment or part over 18 inches long. Other source capture options are available, as well, depending on the size and needs of individual job shops. These include conventional portable or mobile floor models, stationary/wall-mounted models, fume guns and centralized industrial systems (for larger shops).
If the above measures aren’t enough to address safety and compliance issues, using personal protective equipment, such as Powered Air Purifying Respirators (PAPRs), air supply helmets and half-mask respirators is the best option.
Establish proper filler metal storage and handling practices
Taking simple precautions to store and handle filler metals correctly can help job shops get the best performance out of product and minimize costs. Damaged filler metals, including stick electrodes and solid or tubular wire, can cause poor weld quality that ultimately leads to expensive and time-consuming rework. Also, if filler metals become wet or pick up contaminants such as dirt, oil or grease, they need to be replaced.
Filler metals are in sealed packaging when they leave the factory. The first step in keeping them in the best possible condition is to always use gloves when removing them from their original packaging or preparing them for welding, since filler metals can easily pick up sweat from bare hands.
Welding operators should keep filler metals away from areas in the shop where plasma or oxyfuel cutting takes place, as the cutting dust from those processes can accumulate on the surface of solid and tubular wires and cause poor wire feeding. The dust also can clog the contact tip and nozzle on the gas metal arc welding (GMAW) gun, creating poor electrical conductivity and an unstable or erratic arc. Filler metals also should be kept away from water, oil and grease — all contaminants that can lead to poor weld quality, rework or other performance issues.
Storing filler metals properly when they are not in use is important. At a minimum, welding operators should cover the welding wire spool with a plastic bag if it’s left on the feeder overnight. A better practice is to remove the spool from the feeder, place it in a clean plastic bag and close it securely. Store it in a clean, dry area until it’s used again. Using an enclosed wire feeder, when possible, is another good way to protect the welding wire from the environment.
Stick electrodes should be stored in ovens according to the manufacturer’s recommendation.
Implement weld information management
Weld information management is not new to the industry, but it’s a technology that can contribute positively to the efficiency of a job shop. In the past, this technology delivered raw data, and it was up to the user to take that data, interpret it and convert it into actions for meaningful continuous improvement. Often, the effort needed to convert the data into actionable information was too much — especially for a smaller shop that may have limited resources. Technology has evolved to help bridge the gap between data and information, and it requires less manpower.
Welding equipment manufacturers have embedded weld information management capabilities directly into power sources for simplified deployment and management or in some cases, have made the power sources able to be easily retrofitted by adding a module. Weld information management systems that are fully integrated into the power source offer seamless integration and minimal start-up time, and many feature wireless capabilities, so the data is easily uploaded into a computer program. Newer weld information management systems are cloud-based, allowing job shops to access information from the integrated power source or retrofitted module by way of a standard Internet web browser.
The primary categories of weld data monitoring are real-time weld/arc monitoring, which measures defined variables like voltage, wire speed and gas flow; weld data acquisition, which measures, displays and stores defined variables to evaluate specific arc characteristics; and production data, which provides various layers of productivity-related information, including overall equipment effectiveness.
The real value of this technology comes when the production output is compared to acceptable limits or standards so the job shop can identify potential process variances and understand the true cost of the welding operation.
Ultimately, job shops can use this information to increase productivity, improve quality and training and lower operating costs. The data provides many opportunities for continuous improvement and can help shops assess risks and set goals.
Purchase on quality, not price
It’s important to select the best filler metal and equipment for the job, and sometimes this means making a bigger investment. While the up-front cost savings are tempting, cheaper isn’t always better, because it can lead to problems down the road such as poor weld quality and more maintenance.
With regard to filler metals, it’s not uncommon to experience downtime associated with poor wire feeding, excessive spatter or weld defects when using lower-quality products. Job shops may also find themselves spending an excessive amount of time on activities that hinder productivity, such as applying anti-spatter and post-weld grinding or rework. It’s important to look at the total cost of using particular filler metals, as opposed to the per-unit cost. Higher quality filler metals can often minimize labor costs and provide better weld quality and greater productivity.
The same considerations are true when selecting power sources. Less expensive machines may not have the longevity of more expensive, quality equipment, which can result in higher and more frequent replacement costs for job shop fleets. Cheaper machines may also experience more breakdowns, which mean higher maintenance costs and lost productivity. More expensive machines also may offer a more intuitive product interface and better ease of operation, making it easier to train welder operators.
In closing
These tips may involve an investment of time, effort and resources, but they can pay off in productivity and quality gains and reduced costs in the long run for job shops that use a variety of welding processes and equipment. The goal for any shop to remain competitive is to look for practical efficiencies that make it easier to manage their filler metals and equipment, and get the most out of these technologies. Having well-trained and safe employees adds to that goal, instilling a sense of ownership and pride in having a well-run shop.