Pulsed MIG Welding and Metal-Cored Wire Give Arizona Fabricator Contract-Winning Edge
Few would contest that Bell Steel, Inc. has found its niche in the structural steel market. The company tackles the “out-of-the-norm” parts and projects with the speed and accuracy, not to mention the enthusiasm, needed to build a solid reputation for itself. In fact, that willingness to take on challenging projects and finish them quickly, from detailing to fabrication and erection, is what Vice President Brandon Bell says sets the company apart from the competition and makes them most appealing to their customers.
“We don’t do the same thing every day. We like that our customers come to us with a problem and that we are able to fix it,” he explains. “That’s why we don’t just do structural steel buildings. Those are great, but we have the people, the know-how and the attitude to take on some really complex projects. We thrive on those challenges.”

them to complete over 650 inches of weld, per solar array post,
in just 12 minutes compared to two and a half hours by hand.
The AISC-certified company, located in Gilbert, Arizona, prides itself on designing and fabricating projects worldwide – from concept and raw materials to completed, primed and painted components – based almost entirely on word-of-mouth referrals they receive from existing customers. Among the notable projects the company has undertaken is the fabrication of steel beams for the Phoenix Sky Train project, a large transportation expansion at the Phoenix Sky Harbor International Airport being completed in conjunction with train manufacturer, Bombardier.
Bell Steel also recently won a large contract with Construction Product Distributors and Sun Edison Energy that, to start, required them to fabricate over 5,000 posts for solar arrays to be used in a new sun tracker system, with the potential for an additional 10,000-post contract in the coming months. They accomplished the first leg of the task with an investment in new XMT® 450 MPa Multiprocess welders from Miller Electric Mfg. Co. and FabCOR® Edge™ MC metal-cored wire (formerly Tri-Mark® Metalloy® Vantage)from Hobart Brothers. Coupling this technology with a new custom Bug-O side beam system, Bell Steel is now poised and ready for the next big contract that comes its way.
Getting ahead with new technology
When Construction Product Distributors contacted Bell Steel to take on the solar array post project, Bell knew that the sheer volume of the contract and the short turnaround would require investments in new technologies.
According to Bell, each of the 5,000 carbon steels posts needed approximately 658 inches of weld and the company would only have three-and-a-half months to complete the job.
“My initial thought was that there was no way we could do this project by hand,” says Bell.
After contacting productivity specialist Jim Kelly of Praxair Distribution in Phoenix, he agreed that the process would need to be automated to achieve the quick turnaround for this contract. Initial time studies, while the company waited for its new XMT 450 MPa machines and Bug-O side beam system to arrive, confirmed that. Bell recorded how long it took for one of his welding operators to weld one of the 3/8-inch thick posts by hand, welding four five-and-a-half foot long fins onto the pole with continuous quarter-inch welds.
The result? Two-and-a-half hours.
Not surprisingly, when the equipment arrived and was installed, the productivity increases were substantial, especially since the XMT 450 MPa power sources were able to operate seven days a week, 24 hours a day.
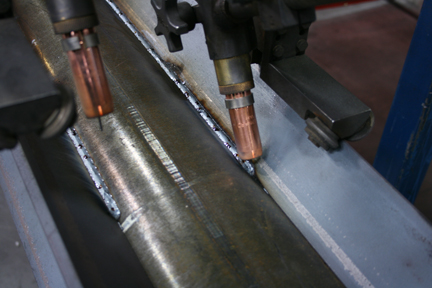
Miller XMT 450 MPa machines provide Bell Steel with high-
deposition, high-quality welds with no spatter, as shown
here. The quality of the welds makes it possible to proceed
to a galvanizing process without post-weld cleaning.
“We knew we needed 100 percent duty cycle. We knew that we needed to be able to run big wire so the process would go faster,” says Bell. “And we knew that the Pulsed MIG technology on the new Miller machines could help us go faster and get that great weld.”
The Miller XMT 450 MPa provides up to 450 amps of welding capacity (Bell Steel operates theirs at just under 400 amps) and, along with the ability to operate at 100 percent duty cycle, it features built-in Pulsing programs that can operate with larger diameter wires, like the 1/16 inch FabCOR Edge MC metal-cored wire selected for the process.
Once implemented, the Pulsed MIG programs found in the XMT 450 MPa proved Bell’s theory to be correct. The machine also provides advanced arc control, which offers more control over the weld puddle and bead characteristics. Bell Steel was able to utilize these settings to widen the arc cone, increase the fluidity of the weld puddle and flatten the weld bead. In addition to gaining faster travel speeds and preventing quality issues like undercut and lack of fusion, those attributes resulted in the desired weld results. According to Bell, the company has had no rejects on the solar array posts using the XMT 450 MPa.
After comparing the results from the manual welding time study with the new system and Miller machines, the results were even better than expected.
“When these machines came in, we were hoping to get one [post] done every 15 to 20 minutes after handling. It worked out better than we anticipated and we were doing one every 12 minutes,” says Bell. “So we could weld one by hand at two and a half hours or one with the machines at 12 minutes with all 650 or so inches of weld.”
The new system also made it possible for Bell to reallocate existing labor throughout the company to work on other projects, since it only required one person to oversee the operation.
He explains, “We were able to use our manpower to do something else that’s productive to help the company, rather than bog them down with just welding all day.”
He also adds that because of the 100 percent duty cycle on the XMT 450 MPa machines, the welding operator overseeing the system needed breaks before the machines.
“When the person overseeing the operation had to take a break, we actually switched out somebody, so the machines never did stop.”
Adding to the benefits with metal-cored wire
Bell Steel also gained additional benefits with its new welding machines through the implementation of FabCOR Edge MC metal-cored wire from Hobart Brothers. Because of the Pulsed MIG programming capabilities of the XMT 450 MPa, the company was able to increase from a .052-inch wire to 1/16 inch, allowing them to put down more wire, in less time, with less heat — ultimately lowering wire cost per pound.
According to Bell, the company is able to operate the FabCOR Edge MC wires at a travel speed of approximately 31 inches per minute (IPM) on two welding guns with no weld defects.
“The product quality and the productivity went up using metal-cored wire because we were able to produce a cleaner weld, faster,” says Bell. “We’ve recently switched over our whole facility to metal-cored wire as a result. We’re using the Hobart Brothers TM-910 for our hand-held operations. Once we saw firsthand the benefits of being able to weld faster and get better looking welds, it was an easy call.”
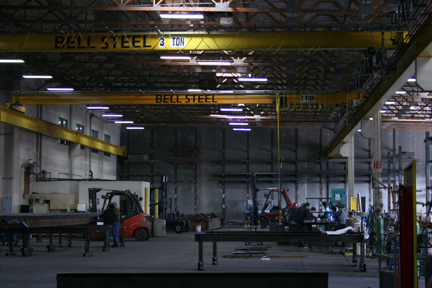
higher quality, greater deposition) on the solar array post
project, Bell Steel has converted the remainder of its welding
operations, including hand-held processes, to the products.
Among the reasons that Bell saw such quality improvements with metal-cored wire is the construction of the wire. Metal-cored wire consists of a hollow metal sheath filled with metallic powders and/or alloys that provide characteristics ranging from arc stabilization to higher tensile strengths. As a result of their tubular structure, these wires carry the welding current though the outside metal sheath, resulting in a broad, cone-shaped arc and a wide penetration profile, as well as high burn-off rates that increase deposition rates and provide faster travel speeds. They also create less spatter, a benefit that Bell noticed right away.
“In the post-weld, we definitely saw a difference. There was a lot less cleanup with metal-cored wire,” he explains. “All of these posts needed to be galvanized so they need to be very clean or the galvanizing wouldn’t adhere.”
A welding system primed for the future
Bell Steel’s investment in the new side beam welding system with the XMT 450 MPa machines and FabCOR Edge MC metal-cored wire yielded results that not only kept them at the leading edge of their commitment to the solar array post contract, but it also opened up additional opportunities for similar contracts. Bell is waiting on word of the success of the solar array project in the field to learn whether they will need to tackle the additional 10,000 posts, but in the meantime, they are ready to use the machines and wire on other similar projects.
“The possibilities with the Miller machines and wire are pretty much endless,” says Bell. “If we have big base plates that need to go on columns with a big continuous welds, we can do that now.”
The total benefits of the system are sure to translate well to the company’s philosophy.
“People know they can come to us with the “not-so-normal” job and we’ll embrace it, make it a win-win situation for everyone and grow with it,” says Bell. ” I think that’s what sets us apart: our attitude and knowing that, from the top down, they have somebody with the attitude and the know-how to be able to take the job from start to finish.”