Investment in Metal-Cored Wire Technology Helps Drive Company’s Success
Few people can say that they’ve had the opportunity to work with three generations of their family or that during that time the work consisted of everything from traditional blacksmithing to modern welding, fabrication and contract manufacturing — all under one roof. Ken Swartfager, owner of Swartfager Welding Inc. can.
Swartfager represents the fifth generation to carry on the family business, and his son, Dustin, is using his position as the sixth generation — along with his knowledge as an engineer — to implement new welding technologies far advanced from those in the company’s beginnings. The results are noteworthy.
“I’ve seen the change here from a forge and basically Stone Age equipment to new, modern technology,” says Swartfager. “Today, we’ve got CNC equipment, robotic welding systems and more that are just great for us. There’s still a place for ‘old school’ equipment, but the new equipment definitely makes welding a more enjoyable field to be in, and it’s helping improve our business.”
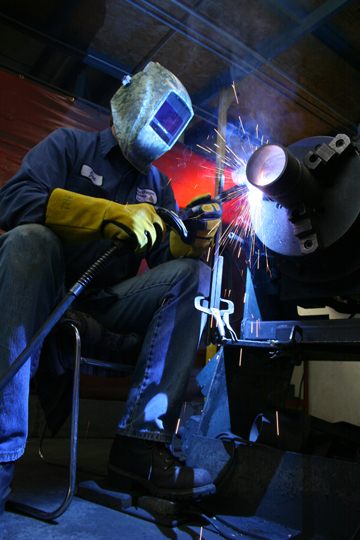
operations has helped simplify training
and certification for welding operators
at Swartfager Welding, even expediting
certification for strict standards such as
Germanischer Lloyd for shipping industry
applications.
In recent years, Dustin has identified metal-cored wire as one of the key technologies to help Swartfager Welding in its continuous effort to improve productivity and quality, and to give the company a competitive edge. He has implemented Hobart ® FabCOR® 86R (formerly branded Tri-Mark® Metalloy® 76) metal-cored wire throughout the facility, on both robotic welding and handheld applications. Combined with advanced welding equipment from Miller Electric Mfg. Co., the wire is helping poise the company for greater growth and continued success.
In fact, the company is currently planning to expand as a means to further ensure the quality of its work. According to Dustin, Swartfager Welding plans to start bringing its materials in-house.
“We want to control every aspect of our work and control the processes from beginning to end,” he explains. “We don’t want to have to worry about supply and quality issues or delays.”
That thought process, adds Swartfager, is keeping with the expectations of its customers.
“We’ve got long-standing customers and the end result they want is quality. These customers are all over the globe and they come here because they know they can always get it.”
From simple beginnings to advanced technologies
Swartfager Welding opened in the 1800s as a blacksmith shop and grew into the manufacturing and fabricating of components for agricultural, rail and mining equipment, both strip and underground. Today, the company has built on those traditions, focusing its work primarily on heavy rail, marine, offshore drilling and stationary power generation applications. Such changes reflect the company’s willingness to adapt to the changing needs of the marketplace, its customers and the current workforce. It also reveals a key philosophy the company has about technology.
“As soon as we find the need for new equipment, we absolutely refuse to not buy the newest there is,” explains Dustin. “We want the best. We don’t want to go back. We don’t want to retrograde any of our machines or our capabilities. We want to be on the cutting edge all the time. That’s the only way we feel we progress.”
Dustin, who has been welding since he was 8 or 9 years old, recognizes that not everyone has the same amount of experience he does, especially given today’s shortage of skilled welders. He sees the willingness to invest in new technology as a way to support the workforce in the Knox, Pa., community where Swartfager Welding is located.
“New technology allows us to bridge the gap if a person doesn’t have a lifetime of work hours in the field,” Dustin explains. “You can take somebody with a good, basic understanding, who might not be as proficient as someone with 10 years of experience, and give them the tools necessary to complete a job. It helps us keep our investment lower to get the same return. Without new technologies, that just wouldn’t be possible.”

spatter-free, minimizing the need for costly and time-
consuming post-weld cleaning.
Finding advantages with metal-cored wire
Dustin learned about metal-cored wire about five years ago when business in the company’s pipe applications area began to increase. Welding operators had been GTAW or TIG welding the root passes on the company’s pipe applications, but the slowness of the process prevented them from maximizing their productivity. The company first tried solid wire as an alternative, but they were unhappy with the quality.
“Solid wire cover passes didn’t look good,” says Dustin. “We had spatter issues and a multitude of problems that were hard to overcome. We weren’t achieving proper fillet shape while out of position. We also had lack of proper fusion from the lower heat setting needed to keep the solid wire in the appropriate spot while being out of position.”
Dustin worked with his welding distributor, Gary Kahle of Matheson Valley Gas (formerly Valley National Gas) in Falls Creek, Pa. to test metal-cored wire next, leading to the implementation of Hobart Brothers Tri-Mark Metalloy 76.
“Metal-cored wire allows us to take about any material, and produce a joint that is structurally better. It looks better and we still keep joint integrity,” Dustin explains.
These benefits come, thanks in part to the structure of metal-cored wire. The wire consists of a hollow
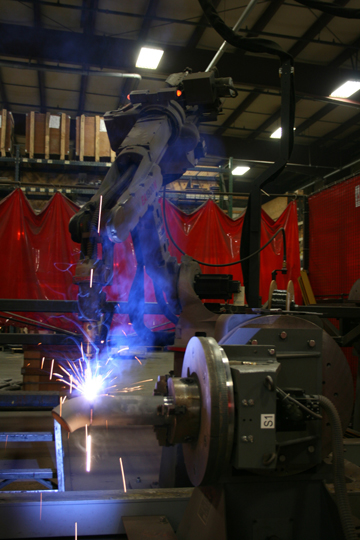
standardize on metal-cored wire throughout
its facility, including in its robotic welding cells.
The company uses the wire for root and cover
passes, and has little to no post-weld grinding
for spatter.
metal sheath filled with metallic powders and/or alloys that provide characteristics ranging from arc stabilization to higher tensile strengths. As a result of their tubular structure, these wires carry the welding current though the outside metal sheath, resulting in a broad, cone-shaped arc and a wide penetration profile that helps ensure consistent weld quality. This structure also makes the technology versatile for multiple applications throughout the company’s welding operations and helps control its inventory.
Swartfager Welding’s inventory now consists primarily of the metal-cored wire in .045- and 1/16-inch diameters, which welding operators use for applications ranging from thin gauge materials to heavy plate and pipe, on which welding operators use a Pulsed MIG program (the PipeWorx® Welding System from Miller Electric Mfg. Co.) to weld out of position. The company also uses the wire in the robotic cell and has been able to simplify its programming since turning to the technology.
“We run it [metal-cored wire] exclusively. We haven’t switched the robot away from metal-cored wire since the first day we hung it on it,” explains Dustin. “We run it on everything that goes into the cell … for the root pass and cover pass. It seam-tracks just as well as anything else and it touch-senses without trouble.”
According to Dustin, the company has also reduced its anti-spatter solution usage on its pipe applications from seven or eight 55-gallon drums annually to one since converting to metal-cored wire.
“Spatter is at a minimum when you’re out of position with Pulsed MIG welding (with metal-cored wires). We probably get a 30 to 40 percent increase in production during the day because we don’t have to go back and grind the spatter off the pipe,” he says.
Advanced standards and quality
In addition to reducing inventory and downtime for post-weld cleanup, metal-cored wires have helped Swartfager Welding improve their weld quality and simplify their welding operator training and certification processes.
The company welds to American Welding Society (AWS) standards, as well as industry-specific certifications, such as Germanischer Lloyd for the shipping industry, which Dustin refers to as “one of the most painstaking things in the world to get an accreditation for.”

|of Swartfager Welding and Gary Kahle of Matheson Valley
Gas (formerly Valley National Gas).
He adds, “We have four or five guys qualified for all of their shipping bureaus so we can provide oil and water critical piping systems for marine applications. Metal-cored wire is our defined process that made it easier to get certified. It took our certification window from normally 18 to 36 months down to about four because every time they sampled our stuff, they couldn’t find anything to balk at.”
The ability to gain such certifications in such a short time frame attests to the quality of the welds Swartfager Welding is producing with metal-cored wire.
“When parts come out of the tooling, we don’t want to machine them ever again,” explains Dustin. “Metal-cored wire helps us control that.”
In all, it took the company about a year to convert all of its applications to metal-cored wire. As Dustin explains, by then the company was “all dialed in and dedicated to it and we really haven’t looked back since.”