Flux-Cored or Metal-Cored Wires: Which is Right for the Job?
As with any part of the welding process, there is no one-size-fits-all solution when it comes to choosing the right filler metal. Still every welding operation has the same goal: to utilize a filler metal that promotes consistent quality, productivity and cost savings.
Gas-shielded flux-cored (FCAW) and metal-cored (MCAW) wires are the most common filler metal choices for fabrication and manufacturing applications. As opposed to stick welding, which requires time-consuming and potentially costly electrode replacement, a continuous wire process using these filler metals helps reduce downtime for spool or drum changeover, and provides faster travel speeds and higher deposition rates to improve productivity.
Making the selection between a flux-cored or metal-cored wire, however, can be confusing. Both filler metals are tubular wires filled with alloying elements that provide beneficial welding characteristics; both require a shielding gas and operate with a constant voltage (CV) power source; and both are available in comparable diameters and packaging, among other similarities. So which is the right one to use? Consider these facts to help make the decision.
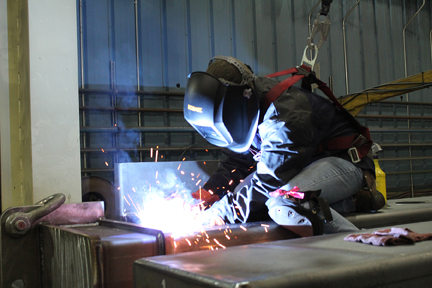
Gas-shielded flux-cored (FCAW) and metal-cored wires are the most common filler metal choices for fabrication and manufacturing applications. It’s important to consider all aspects of the welding operation, from equipment to desired production goals, when selecting between the two.
Gas-shielded flux-cored wires
Gas-shielded flux-cored wires are a good option for applications requiring deep joint penetration on thicker sections of metal, including mild and low-alloy steels found in shipbuilding, railcar manufacturing and heavy fabrication. They offer high deposition rates, and can also be used for welding stainless steel and special alloyed metals like chrome-moly. These wires can operate with either a blend of argon and CO2 or with straight CO2. Because they require gas, however, they are best suited for a shop setting where portability of the gas cylinders is not an issue. Flux-cored wires are popular for both semi-automatic and robotic welding applications, and offer the advantage of being formulated for all-position welding. To gain the best results, these wires operate by way of a drag technique to prevent slag inclusions regardless of the process. Their deposition efficiency — the weight of the weld deposit compared the total weight of filler metal used during welding — falls into the 82 to 85 percent range, which helps support high productivity goals. The loss of weight in this equation can be primarily attributed to smoke, spatter and/or slag. These wires can be used for single- or multi-pass applications, but because they produce slag, the welds require cleaning in between passes.
For companies with applications requiring low hydrogen levels, such as welding on high-strength steel, flux-cored wires are often a very good choice. Filler metal manufacturers can typically formulate flux-cored wires with hydrogen levels as low as 4ml per 100g of weldment, which helps reduce the risk of hydrogen cracking.
Metal-cored wires
Like flux-cored wires, metal-cored wires offer good deposition rates, along with even higher deposition efficiency — approximately 96 percent. They are a good choice for improving productivity on single-pass applications longer than 3 inches that currently employ solid wires. Metal-cored wires offer faster travel speeds and bridge gaps more readily than solid wire, allowing them to increase throughput and reduce potential quality issues, particularly on joints with less-than-ideal fit up. These wires are limited to welding in the flat and horizontal position unless paired with a power source that provides pulsing capabilities. Applications requiring a lot of out-of-position welds may benefit from a flux-cored wire instead, as even with pulsing metal-cored wires don’t always offer as fast of results.
One of the biggest benefits of metal-cored wires is the ability to reduce pre- and post-weld activities like grinding, sandblasting or chipping slag. They are able to weld through mill scale, dirt and debris and the spray transfer mode they utilize produces little to no spatter, reducing the need for pre- and post-welding cleaning. They also require minimal, if any, interpass cleaning so they work well on multi-pass robotic welding applications where high levels of arc-on time are desired. These wires do tend to cost more than flux-cored or solid wires, but many companies find that the quality and productivity improvements negate the higher per pound expense when it comes to the bottom line.
As with flux-cored wires, metal-cored wires are available in the marketplace for welding mild, low alloy and stainless steels, and in low hydrogen varieties. They are well suited for applications in the manufacturing industry, particularly automotive and heavy equipment production, and operate with an argon/CO2 shielding gas blend. The very smooth and stable arc created by metal-cored wires makes them appealing to many welding operators who weld in semi-automatic applications, and the broader arc cone offers a wider penetration profile and consistent weld bead, particularly compared to solid wires.
Making the selection
When weighing out these similarities and differences between flux-cored and metal-cored wires, it’s important to look at the existing process to determine where a company wants or needs to make improvements. For out-of-position applications where high deposition rates are desired, flux-cored wires may be a good way to boost productivity, while companies with solid wire operations seeking to make quality and productivity improvements can likely benefit from metal-cored wires. It’s important to always look at the available equipment, the skill set of the welding operators (along with the ability to provide training opportunities) and the overall production goals when making a filler metal selection. In many cases a trusted welding distributor or filler metal manufacturer can help along the way.