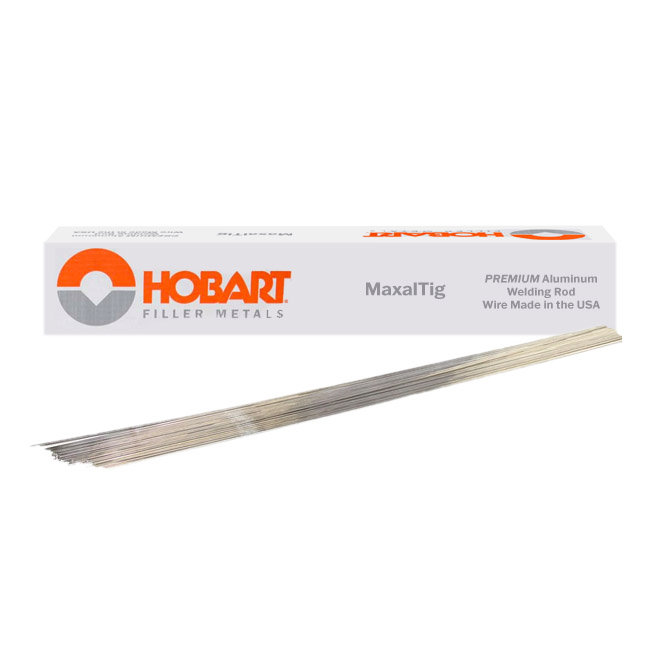
Hobart® MaxalTig® 5356
5356 filler metal is the most common aluminum/magnesium alloy for general purpose welding and is typically used in the construction industry in fabricating truck trailers, small fishing boats, and in …
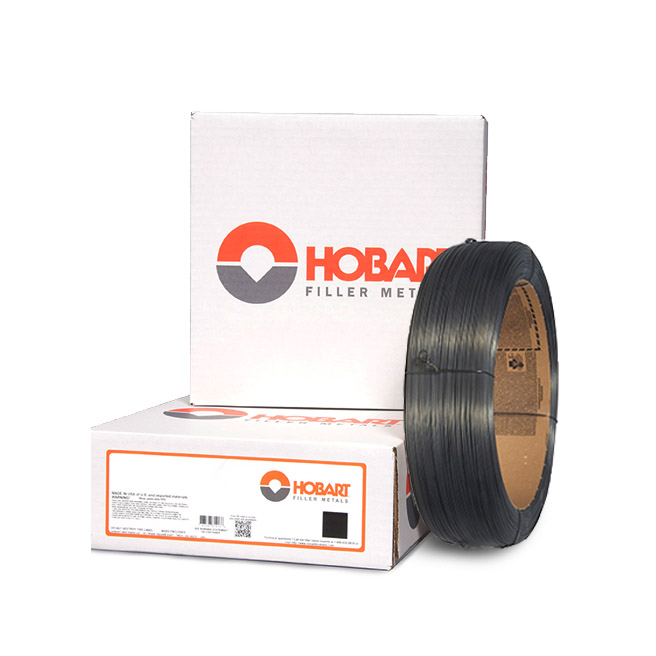
Tube-Alloy® 242-S MOD
Low alloy medium hardness martensitic deposit. Used where maximum abrasion resistance and machinable deposit are required.
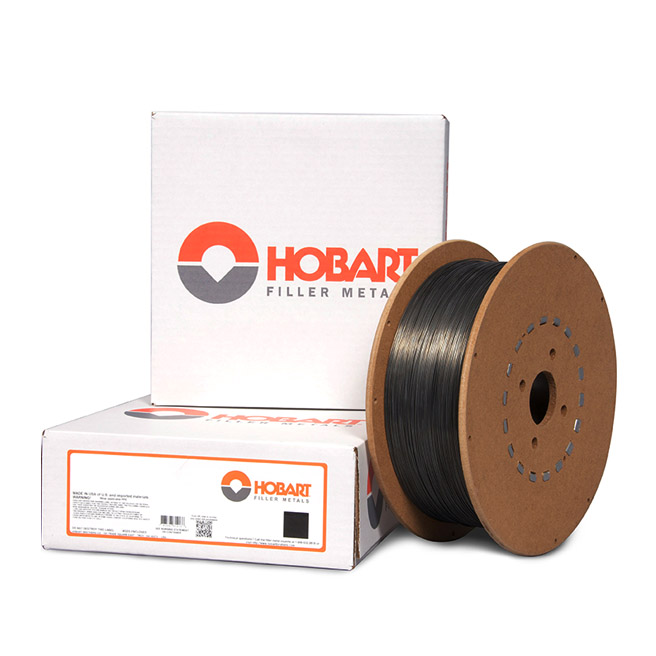
Tube-Alloy® 244-O
The deposit is a medium alloy carbide steel. Designed primarily for the automatic rebuilding of dredge pump shells
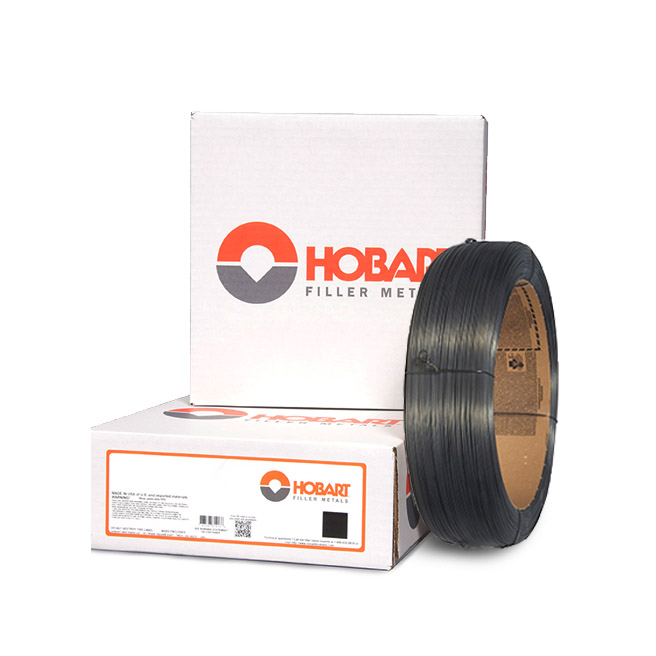
Tube-Alloy® 865-S MOD
A modified stainless steel composition. Provides good metal-to-metal wear, corrosion, and the ultimate resistance to thermal fatigue fire cracking frequently encountered by steel mill rolls.
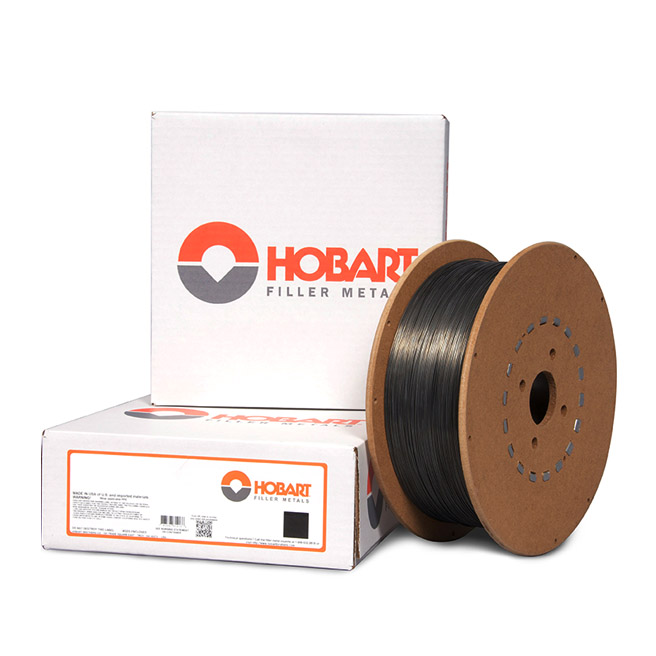
Tube-Alloy® 887-S
A premium martensitic stainless alloy offering good resistance to metal-to-metal wear, corrosion and thermal fatigue.
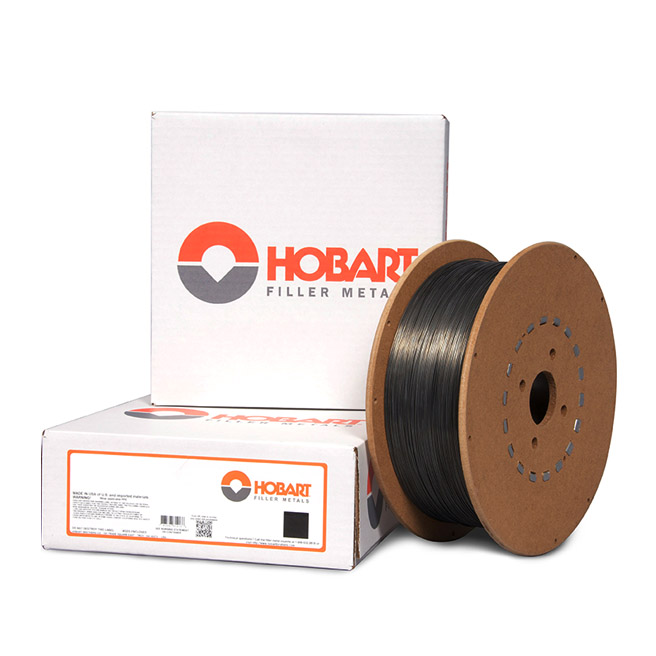
Tube-Alloy® 952-S
Premium modified high carbon martensitic stainless steel with higher hardness than 420. Used for applications where higher impact toughness is required along with moderate abrasive wear.
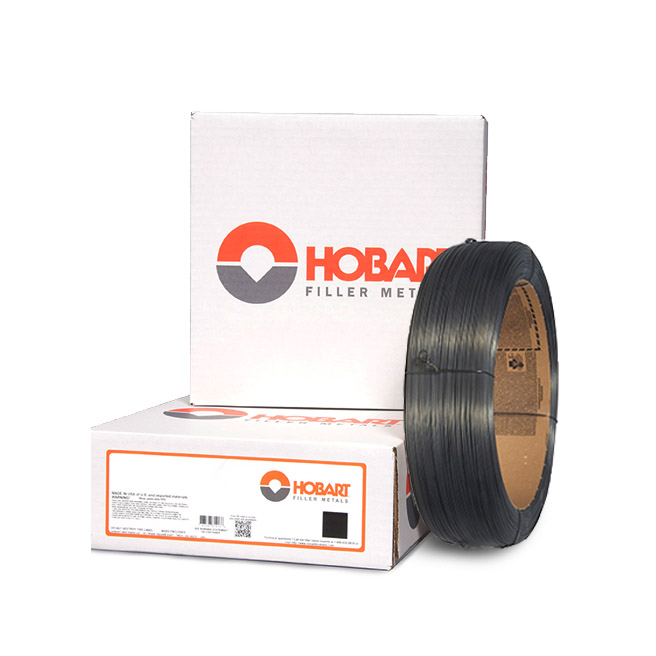
Tube-Alloy® A250-S
A modified 420 stainless steel composition. Good resistance to cracking and corrosion encountered by steel mill rolls
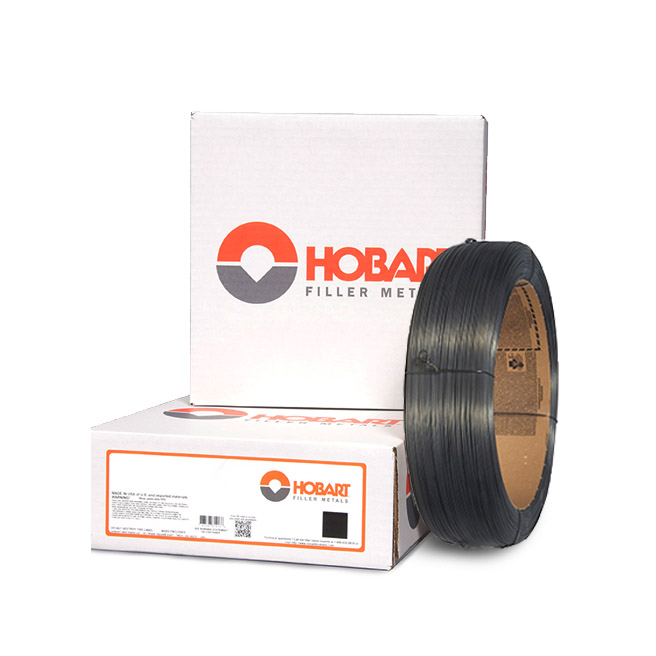
Tube-Alloy® A2JL-S
Modified stainless steel composition. Good resistance to metal-to-metal wear, corrosion and thermal fatigue fire cracking.
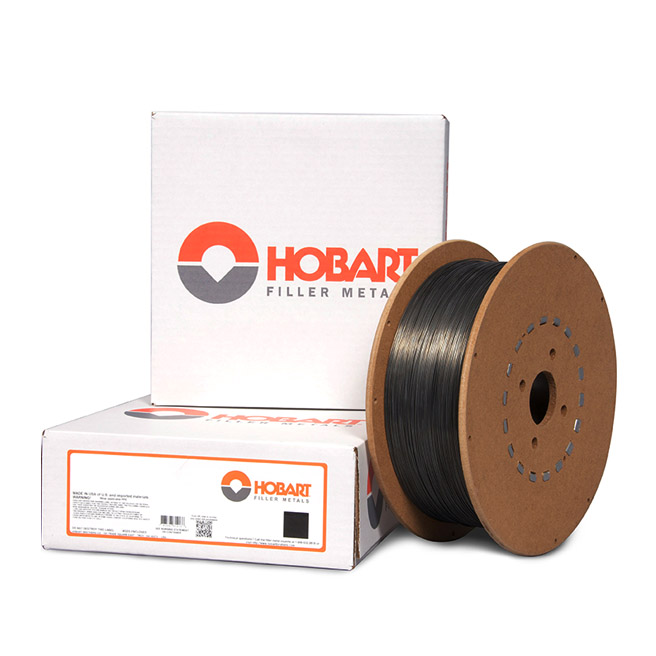
Tube-Alloy® Build UP-G
This product is a low alloy steel deposit. Formulated for build up on mild and low alloy steels only. Offers great compressive strength and impact resistance making it an excellent base for abrasion r…
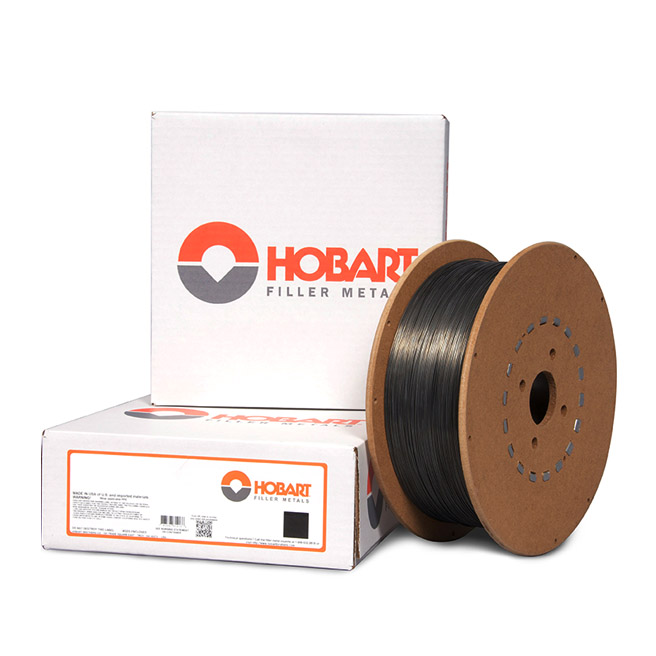
Tube-Alloy® Build UP-O
This is a low alloy steel deposit. Designed for build up on mild and low alloy steels only. Has good compressive strength and impact resistance making it an excellent base for abrasion resistant alloy…
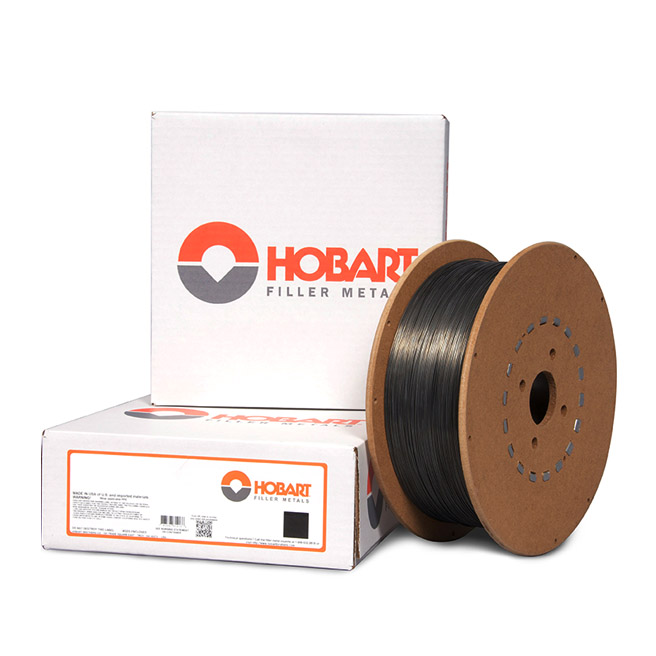
VertiWear® 600
Used for surfacing mild and low alloy components subject to moderate abrasive wear and medium to high impact.

Pipemaster® 70
An excellent all-position, cellulosic mild steel electrode needed for a strong, dependable , X-ray quality weld. It delivers the arc stability and drive you need for the best penetration position; pl…

Pipemaster® 80
An excellent all-position, cellulosic mild steel electrode that delivers the arc stability and drive you need for the best penetration possible. Quick to start, it provides you with excellent wash-in…

Pipemaster® Pro-60
Designed to provide outstanding arc stability, penetration, and wash-in for use on the following API 5L steels: Grade A,B, X-42, X-46, X-52, X-56 and for the root pass on material up to X-80

Quantum Arc™ 3
Solid wire great for general fabrications operations using CO2 or Argon rich shielding gases

Quantum Arc™ 6
Higher deoxidizers allow this product to be used in applications that may have light rust or mill scale.

Quantum Arc™ D2
A high-strength, copper-coated, mild steel solid wire that provides X-ray quality welds when used on carbon and low alloy steels. Produces a high-quality weld that is virtually porosity and slag free…