Oct 16, 2014
New Hobart Metal-Cored Wires Provide Strength After Extensive Stress-Relief Hold Time
TROY, Ohio. October 15, 2014 — Hobart has introduced two new metal-cored wires formulated to maintain strength after extensive stress-relief hold time when welding 4130 and 4140 steels. The Hobart® FabCOR® 4130 SR is a gas-shielded metal-cored wire for semi-automatic welding, and the Hobart SubCOR® 4130 SR is a metal-cored submerged-arc welding electrode. The two wires share similar characteristics, most notably the ability to maintain mechanical properties such as hardness during long periods of stress relief.
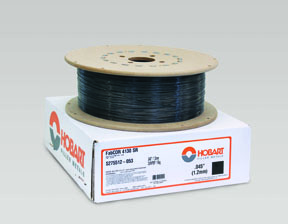
Both wires provide higher deposition rates than solid wires, assisting in increased travel speeds and improved productivity. The wires also offer a high-strength weld deposit with versatile chemistry, making it suitable for use in a range of joining and repair applications with a variety of materials, including AISI 4130 and 4140.
Formulated and intended for use with DCEP polarity, the wires can be used in single and multi-pass welding applications found in the oil and gas and offshore industries; wellhead fabrication and repair; and those using high-strength low-alloy steels.
Like other Hobart metal-cored wires, the FabCOR 4130 and SubCOR 4130 wires offer excellent arc characteristics that result in consistent welds and reliable gap-bridging capabilities.
The FabCor 4130 SR exceeds AWS minimum specifications by offering a tensile strength of 107,000 psi and a yield strength of 98,000 psi, when operating with a shielding gas of 80 percent argon and 20 percent CO2. The wire also offers Charpy V-Notch impact values of 30 ft-lb. at temperatures of -60 degrees Fahrenheit (-50 degrees Celsius). The FabCOR 4130 wire is available in .045-inch diameter, packaged on a 33-pound spool.
The SubCOR 4130 SR is available in diameters of 3/32 inch, 1/8 inch and 5/32 inch, packaged in 60-pound coils or 600-pound drums.