Transportation
The World Relies on Transportation to Get Where They Need to Go. Transportation relies on Hobart® filler metals.
Endurance. Safety. Transportation requires nothing less than the best. To ensure you meet your customer’s needs, you need filler metals that you can count on: Hobart® filler metals.
Deficient welds can put your transportation production at a standstill.
Quality is the key to long-lasting vehicles & trailers, so make sure you choose the best materials for the job. Hobart filler metals offer a large selection of filler metals that will ensure your customer gets from point A to point B time and time again, just like we did for E-Z-GO Carts.
It’s the tie that binds ENDURANCE + SAFETY
E-Z-GO Carts relies on filler metals from Hobart to ensure quality and safety for their golf carts, industrial, and utility vehicles. See why they trust in Hobart filler metals to help produce the #1 golf cart in the world.
Products
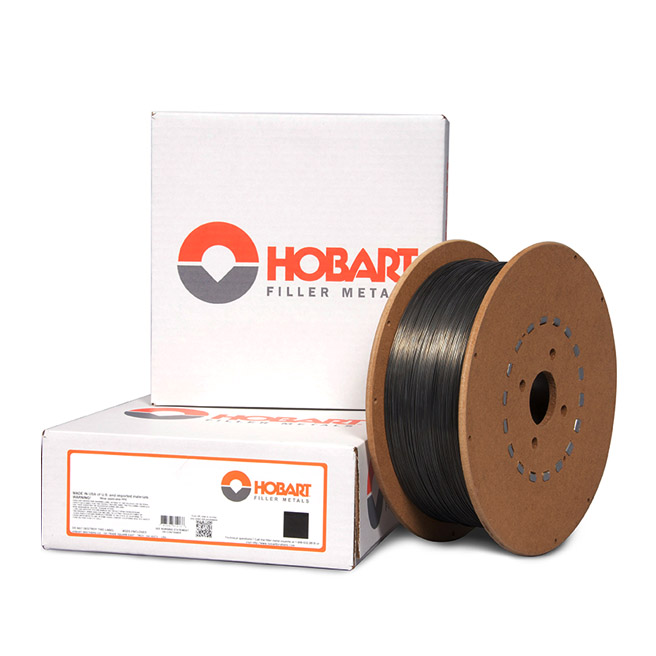
FabCOR® Edge™ XP
AWS: A5.18: E70C-6M H4; A5.28: E80C-G H4
FabCOR Edge XP is a premium gas-shielded metal cored wired that offers X-CEPTIONAL Performance and Productivity. FabCOR Edge XP delivers the high deposition rates and low spatter you expect from a metal-cored wire, plus excellent weld pool fluidity and balanced arc characteristics from which welders of all skill levels can benefit. FabCOR Edge XP’s best-in-class silicon gathering and weld bead contouring help you do great work—and more of it—in less time.
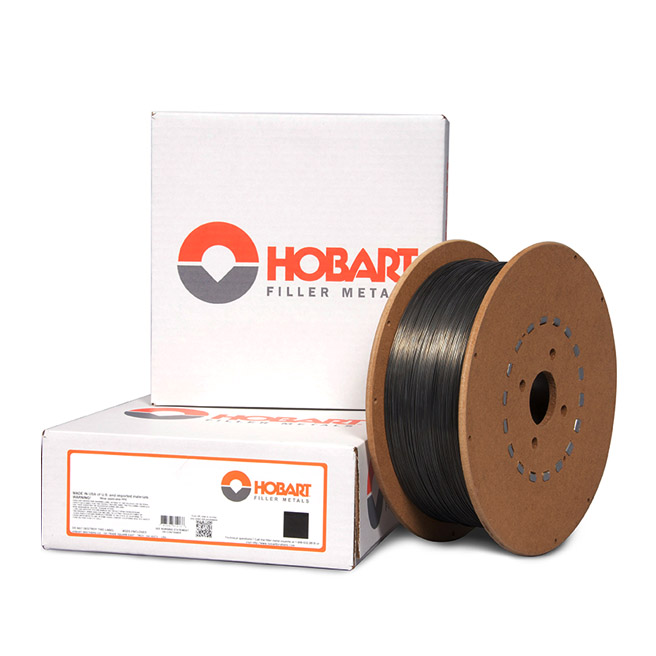
FabCOR® 86R
AWS: A5.18: E70C-6M H4
Higher deoxidization elements allow this metal cored wire to have more tolerance for mill scale welding applications
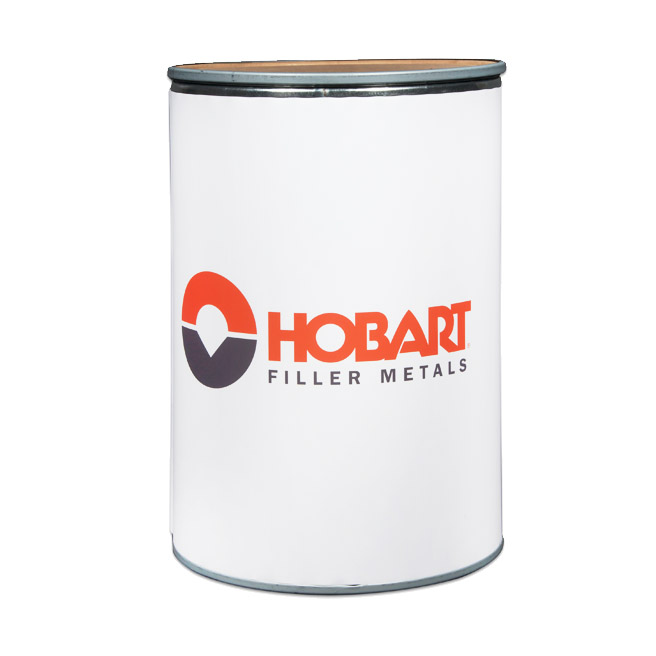
FabCOR® F6
AWS: A5.18: E70C-GS
Extremely high deposition metal-cored wire designed primarily for Automotive and galvanized applications. Innovative formulation results in higher deposition rates than solid wire, excellent gap-bridging capabilities, and a very high-strength deposit that maintains excellent ductility and impact toughness. Designed for use with DCEN polarity.
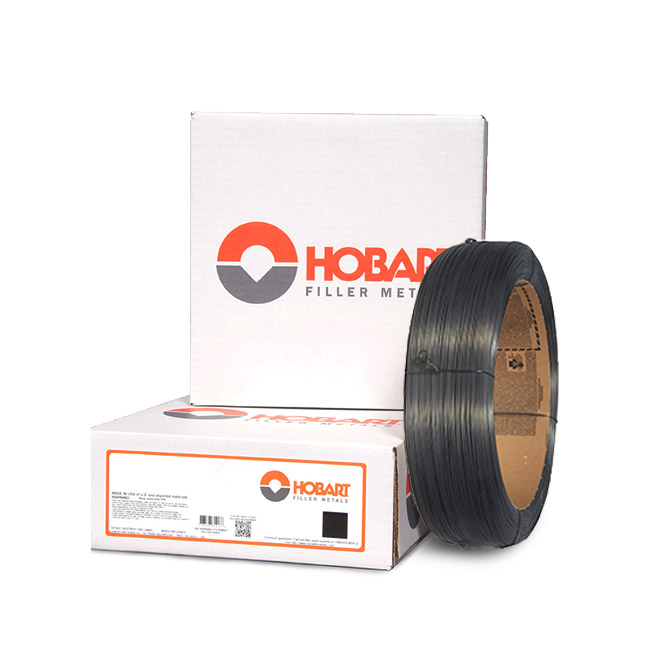
FabCO® RXR
AWS: A5.20: E70T-1C/-9C
RXR is an E70T-1 wire that has a higher level of de-oxidizing elements to handle mill scale, rust and other contaminants.
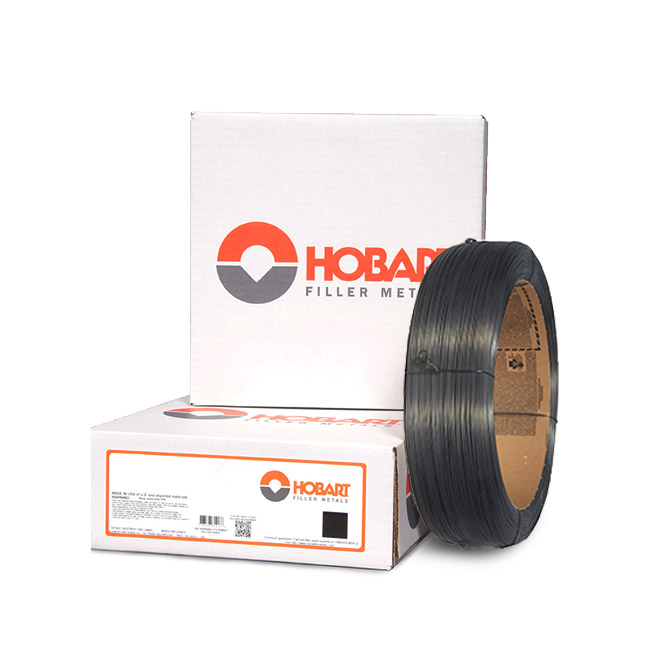
FabCO® TR-70
AWS: A5.20: E70T-1C H8/-9C H8
This wire has low smoke, spatter and excellent operator appeal For mild and some low alloy steels.
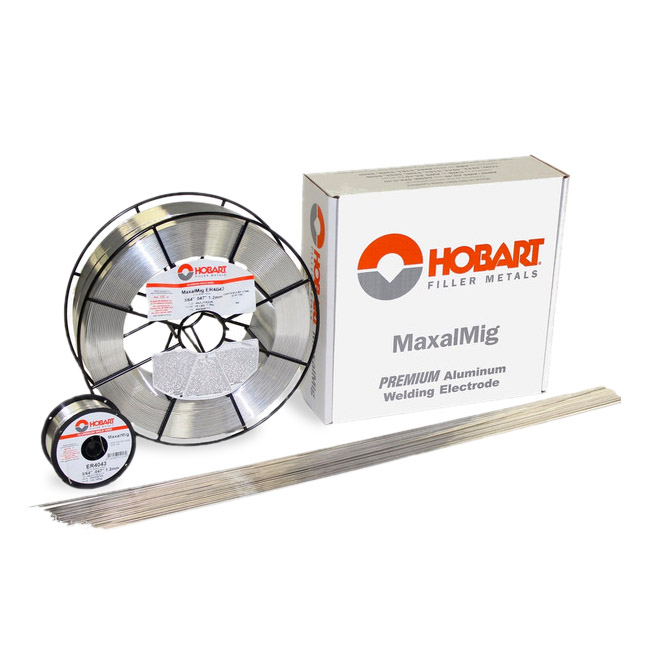
Hobart® MaxalMig® 4943
AWS: A5.10: ER4943, R4943
Alloy 4943 filler metal was formulated to be welded with the same weld procedure specifications as 4043 and 4643, and does not depend upon dilution from the base metal during welding to increase the strength of the weld deposit, while maintaining the same weld characteristics and benefits of 4043 and 4643. Features/Benefits: – 25% higher UTS & 50% higher yield strength than 4043 in the as welded condition (typical) – Moderate/high strength (35 ksi typical) – Low melting temperature/high fluidity – Low welding smut and discoloration – Low ductility, formability, and lower toughness (similar to 4043) – Moderate electrical conductivity and thermal conductivity – Post weld fully heat treatable requiring no base metal dilution – Excellent corrosion resistance – Low shrinkage rate/reduced distortion – Low hot cracking sensitivity in most applications
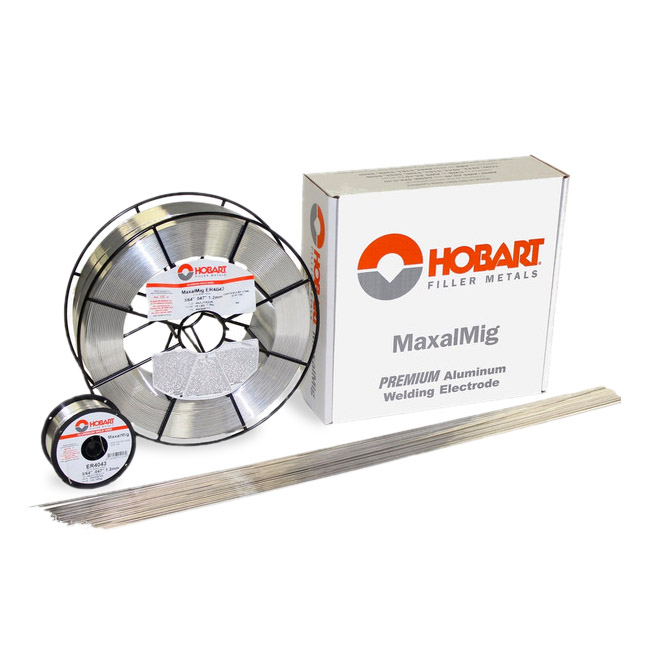
Hobart® MaxalMig® 5356
AWS: A5.10: ER5356, R5356
5356 filler metal is the most common aluminum/magnesium alloy for general purpose welding and is typically used in the construction industry in fabricating truck trailers, small fishing boats, and in cryogenic applications. Features/Benefits: – High strength (38 ksi typical) – High ductility/fatigue strength/very high toughness – Moderate ductility/formability – Lower electrical conductivity and thermal conductivity – Higher column strength/better feedability – Very good color match after anodizing with 5xxx/6xxx base materials
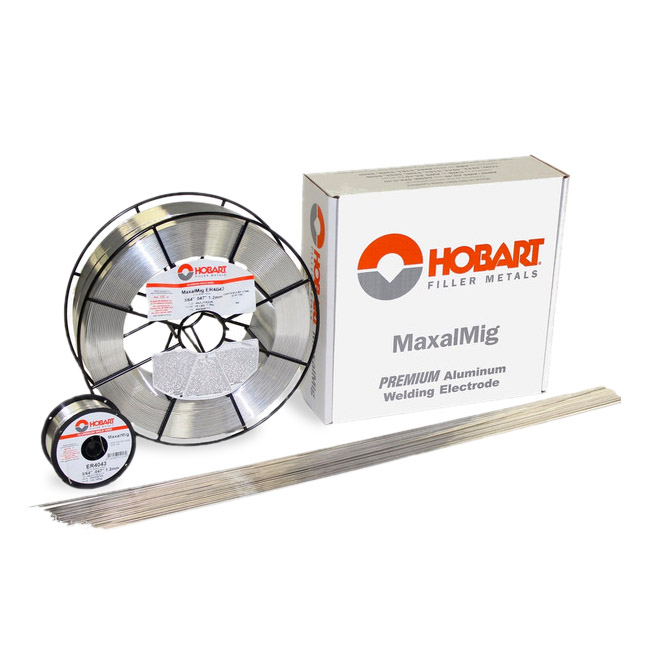
Hobart® MaxalMig® 4047
AWS: A5.10: ER4047, R4047
Common applications for 4047 are for thin sections where the higher fluidity and lower shrinkage rate are important for distortion control. 4047 is also used in applications where excellent wetting action for joint sealing of pressurized fluids and gases is required. Features/Benefits: – Low melting temperature/high fluidity – Excellent wetting action for joint sealing applications – Low welding smut and discoloration – Very low ductility, formability, and toughness – Moderate electrical conductivity and thermal conductivity – Excellent corrosion resistance – Very lowest shrinkage rate/reduced distortion – Low hot cracking sensitivity in most applications