Leading Steel Fabricator Gains Productivity and Cost-Savings with Metal-Cored Wire
For more than 70 years, LeJeune Steel Company has been an industry leader in steel fabrication. In that time, the company has grown into one of the largest structural steel fabricators in the Midwest, with more than 40,000 tons of steel fabricated each year at its facilities in Minnesota and Wisconsin.
LeJeune built the roof trusses for the U.S. Bank Stadium in Minneapolis, which will become a venue for Minnesota Vikings football games, large concerts, the 2018 Super Bowl and the Final Four in 2019. The stadium encompasses 38 acres, takes up 1.5 million square feet and will offer 65,000 seats. To be better equipped for demanding jobs like this one, LeJeune relies on Hobart® metal-cored wire. The company converted to this filler metal technology in 2008, when LeJeune shop manager Tim Crews began talking with the company’s distributor, Dave Becker of Oxygen Service Company.

become a venue for Minnesota Vikings football games, large concerts, the 2018 Super
Bowl and the Final Four in 2019. The stadium encompasses 38 acres, takes up 1.5
million square feet and will offer 65,000 seats.
Becker explained to Crews that LeJeune could potentially cut down on production costs by converting from flux-cored wire to metal-cored — it requires less cleanup, offers better deposition rates and generates less smoke. In the end, he explained, this filler metal would cost slightly more upfront, but actually cost less than the flux-cored wire overall due to these benefits.
“We started developing a plan to put together, which involved the Hobart Toolbox,” Becker says. The Toolbox is an assessment program that helps analyze the cost and efficiency of a welding operation.
Becker and Crews first took inventory of all of the welding machines LeJeune had in the shop, calculating how many feet of flux-cored wire it used in a given amount of time. Next, they compared that formula to the metal-cored alternative by sampling 8,500 feet of welds and conducting a time study with the new wire. The result?
“We found that the metal-cored wire had about a 20 to 25 percent better deposition rate and definitely required less cleanup — as far as no spatter,” Becker says. “Tim also noticed that we didn’t need air-powered chipping hammers since there was no slag to remove.”
Welding operators noticed that the shop was quieter without the noise from the chipping hammers and also that the wire’s formulation generated less smoke.
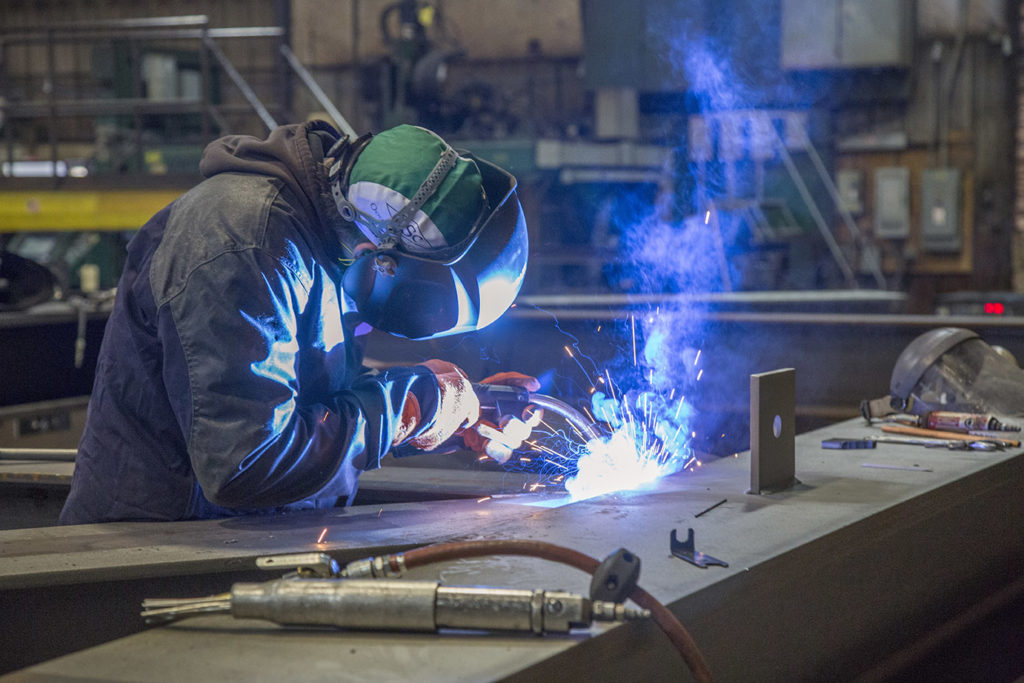
per 8,500 feet of welding with metal-cored wire, based on
increasing deposition rates, minimizing downtime to clean
spatter and reducing waste for wire breaking before welding.
“We had to tweak some parameters, as far as the operating window of how many volts and amps — we had to make sure everybody stayed inside that window,” Becker says. “But the welding operators seem to like it. They like the less smoke, and they like that they don’t have to clean up weld spatter and slag from the flux-cored process.”
What is metal-cored wire?
Metal-cored wire is a tubular wire filled with metallic powders, alloys and arc stabilizers that provide benefits such as lower oxidation, higher impact strengths and reduced silicon deposits in the final weld. The alloys inside the metal-cored wire vary, depending on the properties and characteristics it provides.
Like flux-cored wire, metal-cored wire has a tubular construction and offers higher deposition rates than solid wire. However, unlike flux-cored wire, it does not contain any slag-producing elements. This feature makes it more efficient, because more of the wire ends up deposited in the joint as weld metal. Low spatter levels and the lack of slag also contribute to the time- and cost-saving benefits by minimizing cleaning activities such as grinding and chipping.
Metal-cored wire operates in the spray transfer mode and works well for flat and horizontal welding applications like LeJeune typically encounters; it can, however, be used out-of-position with a pulsed welding process. During welding, the current travels through the outside metal sheath of the metal-cored wire, allowing it to produce a broad, cone-shaped arc, create a wide penetration profile and bridge gaps easily. The wire’s construction also allows for greater travel speeds so LeJeune’s welding operators can complete welds faster and meet the company’s strict deadlines.
Flux-cored versus metal-cored wire
LeJeune first began looking for an alternative to flux-cored wire in order to find a cleaner wire for environmental reasons and to reduce waste.
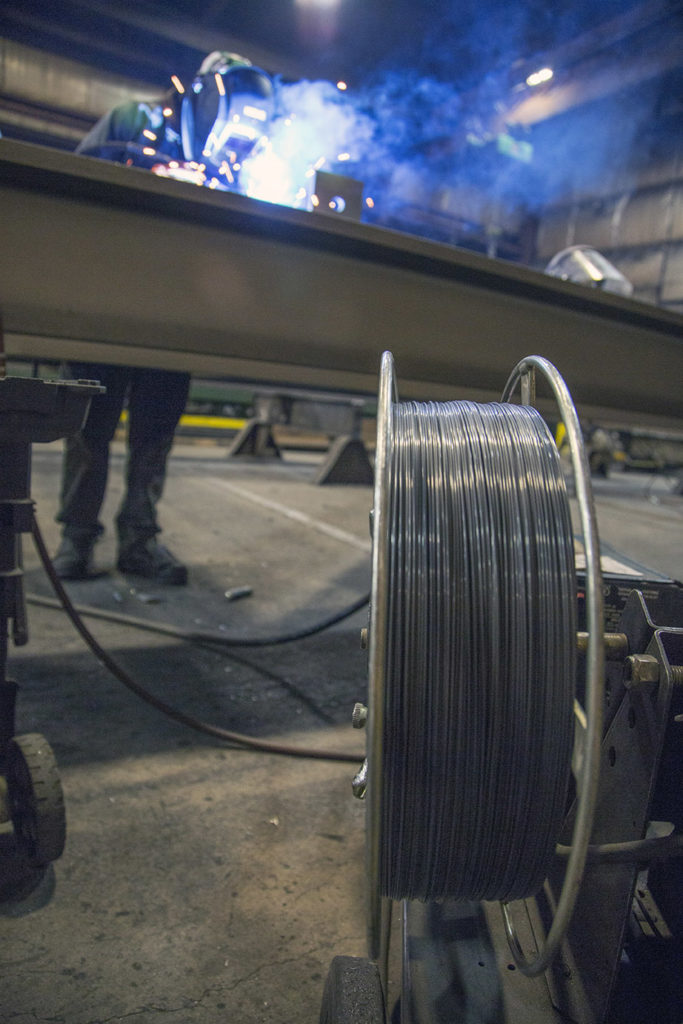
welding applications like LeJeune typically encounters
and its construction allows for greater travel speeds
so welding operators can complete welds faster and
meet the company’s strict deadlines.
“We found that with the flux-cored wire, the guys were breaking off wire,” Crews says. “With metal-cored wire, we don’t have to do that anymore. We can stop and start welding without breaking off wire, so we waste less and use less wire.”
Jeff Organ, the quality control manager at LeJeune, sees additional benefits to using metal-cored wire, too. “You don’t have the slag. You don’t have the delay. You’ve got immediate results,” he says. “You don’t have a lot of cleanup to deal with, which is very beneficial, and the deposition rates are better. In other words you get more pounds down per hour of actual arc time.”
The conversion process
LeJeune Steel Company’s conversion from flux-cored to metal-cored wire required several steps.
First, the company needed to determine what wire to purchase. The team sampled several brands and ultimately decided to buy the Hobart FabCOR® 86R metal-cored wire because “our guys liked the way it ran,” Crews says.
“The way the glass [silicon] would pop off and form in the center of the weld — it popped right off and they didn’t have to clean it,” he says. “It was just easier to use.”
Next, the company needed to switch from straight carbon dioxide shielding gas to a mixture of argon and carbon dioxide, which required a new delivery system, including a carbon dioxide manifold and a gas mixer.
Finally, the company chose to upgrade to higher amperage welding guns to better accommodate the welding parameters for the metal-cored wire. Even after factoring in the costs of these upgrades, Becker and Crews still calculated — based on the company’s labor rate per hour — that LeJeune would save an average of $50,000 per year per 8,500 feet of welding each month.
The stadium project
Most recently, LeJeune has relied on metal-cored wire to complete a portion of the structural steel work for the U.S. Bank Stadium, specifically the roof trusses and catwalks. This two-year project required the fabrication of trusses ranging from 15 to 80 feet long, weighing between 10,000 and 115,000 pounds.
The work included a significant amount of full-penetration welds that are up to 6 inches long and some bracing welds that are up to 8 inches in length. It also required a lot of ultrasonic testing (UT) work and fillet welds. Most of the welds range from 5/16 inches to a half-inch.
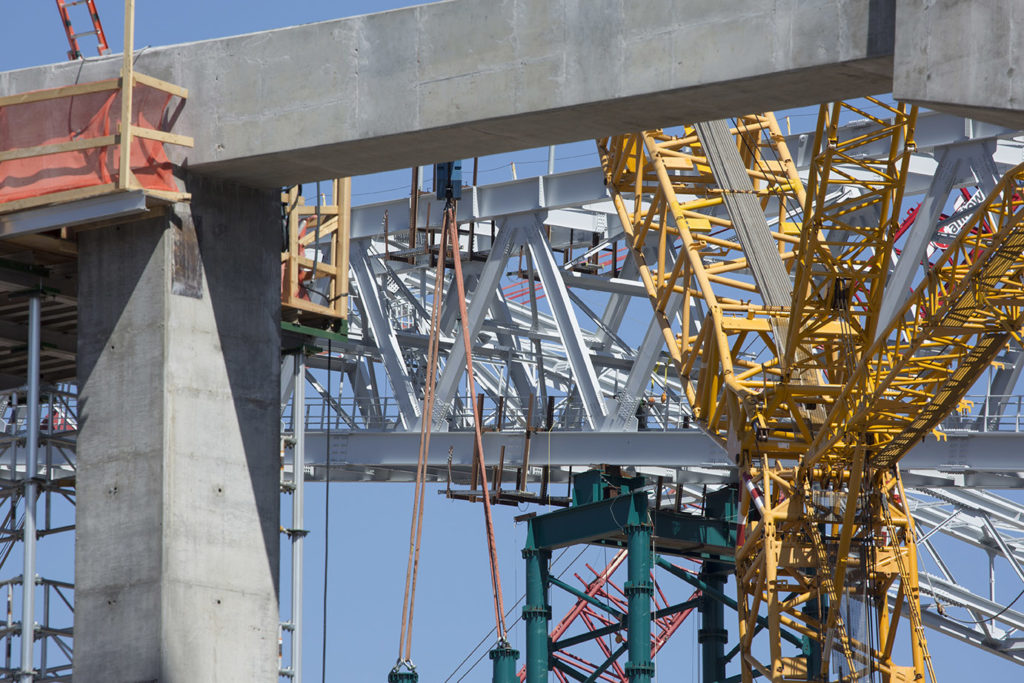
LeJeune that required the fabrication of trusses ranging from 15
feet to 80 feet long, weighing between 10,000 and 115,000 pounds.
The biggest challenges of the job were safety and the sheer size of the project — especially related to moving around heavy steel nearly every other day with multiple cranes. Deadlines are also critical and metal-cored wire’s benefits made it easier to meet those due to the faster travel speeds and cleaner welds it produces.
To complete the work on one truss, it took an average of three days, and the work was completed by three groups of two. In phase one, most of the welding took place. In phase two, the team put the halves together and, in phase three, the groups built the box.
The outcome
For the U.S. Bank Stadium job and the other jobs that LeJeune takes on, metal-cored wire continues to provide the results the company desired going into the conversion.
According to Crews, the company’s productivity has increased by about 20 percent because welding operators are “welding more and cleaning welds less.”
“There’s the stuff that we can put on paper, like the deposition rates and the cleanup time,” he says. “But there was also stuff that we didn’t really count on: wear and tear on our equipment that we had with the flux-cored wire — from the air hammers and air chippers down to the air lines we don’t have to drag across the floor anymore. It’s all been a welcomed change.”
Watch videos
LeJeune Steel Company Increases Productivity by 20 Percent with Hobart Metal-Cored Wire
LeJenue Steel Relies on Hobart Metal-Cored Wire to Meet Project Delivery Demands