SMAW: The Low Down on the Lingo
When it comes to shielded metal arc welding (SMAW), following formal welding procedures is critical to achieving quality results and meaningful productivity. The manner in which welding operators talk about the process, however, isn’t always so formal. Lingo related to equipment, technique, arc characteristics and more are common throughout the industry. In many cases, you won’t find these definitions in your standard welding glossary. Still, they are a prevalent part of the culture of welding.
To help you navigate your way through the lingo, we’ve provided some of the more common terms you might encounter.
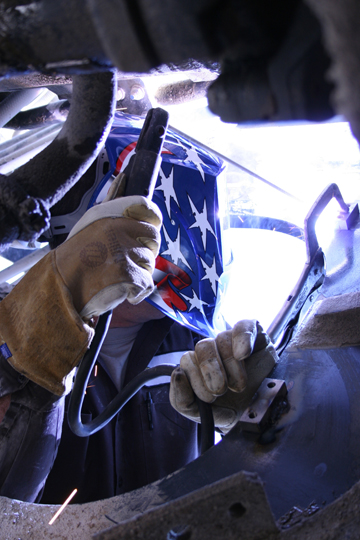
arc characteristics are common throughout
the industry. These terms aren’t critical to
achieving good welds, but they can help you
avoid confusion on the job floor or in the field.
About the weld beads and pools
It’s not surprising that there is so much lingo related to the weld and the weld pool. After all, they are at the core of the process. Here are some terms you may encounter on the job site.
Stringer bead – A narrow, straight weld bead that is created by moving the SMAW electrode straight along the weld joint. A quality stringer bead should have good tie-in on both sides of the weld.
Wetting-out – The ability of a weld puddle to flow evenly, allowing both sides of the weld to merge smoothly with the base material.
Root Pass – The first weld bead placed in the weld joint in a multi-pass weld.
Fill – Also referred to as a fill pass, it is the amount of weld bead necessary to fill the weld joint. This pass comes after the root pass and before the cap pass (see next). In some applications, multiple fill passes are necessary.
Cap – The final weld bead in a weld joint. It may be completed in the form of a stringer bead or by a weaving motion back and forth.
Fisheye – Refers to the shape of the puddle while welding. It is sometimes also used to describe the shape of the crater at the end of the weld.
Keyhole – Refers to the shape of the hole that is formed while welding an open root joint, particularly with an AWS 6010 SMAW electrode. It allows for good penetration and tie-in in the completed weld.
All about the arc
Arc characteristics are important in any welding process. These allow the welding operator to determine travel speed and motion or method to move the SMAW electrode to gain the desired results. These terms all refer to the arc or technology used to adjust the arc for improved performance.
Stiff – Refers to an arc that provides a lot of drive (dig) into the weld joint. It can often be associated with increased spatter.
Soft – Refers to an arc that has less drive (dig) and potentially less penetration into the weld joint.
Dig – Another term for arc force or arc control, it offers the ability to adjust the drive of the SMAW electrode to gain more or less penetration into the weld joint.
Arc Control – The ability to adjust the amount of dig for the best weld result. It also refers to the technology that provides the power source with additional amperage during low voltage (short arc length) conditions. In this case, it helps avoid “sticking” the SMAW electrode when a short arc length is used.
Hot Start – Function used on some SMAW power sources to simplify arc starting when using difficult-to-start electrodes. It works by adding additional current to help establish the arc.
Arc Blow – Refers to the deflection of the arc away from the direction of travel, due to either magnetic or thermal influences. For example, as the weld gets closer to the end of a plate, it may be directed to one side, forward or backward, typically resulting in heavy spatter and undercutting. Arc blow caused by magnetic build-up is also referred to as arc wander.
Define your technique
Creating quality welds during the SMAW process requires special attention to welding parameters and procedures. It also demands attention to various welding positions. Across various industries, the following are some common related terms you may encounter.
Downhill – The technique of creating a weld in a vertical down progression, i.e. from “top to bottom” of the weld joint.
Uphill – The technique of creating a weld in a vertical up progression, i.e. from “bottom to top” of the weld joint.
Weave – Also referred to as “oscillating or stitching” it is the technique of moving the SMAW electrode from side to side in order to wash the sides of the weld pool into the base material.
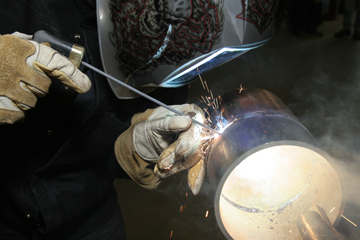
to SMAW refers to common occurrences you may encounter
in the process.
What to call weld defects?
Weld defects are an unfortunate reality in any welding process – and one that proper technique and adherence to welding parameters can help prevent. When these problems do occur, however, some in the industry call common weld defects by these terms.
Cold Lap – A weld defect that occurs when there is lack of penetration on one leg of the weld. It is also called lack of fusion or incomplete fusion and is most often caused by too slow of travel speeds or too wide of weave during welding. It can also be caused by lack of heat input, which prevents the weld and base metal from fusing together.
Undercut – A weld defect in which there is an overhang of the base material to the weld bead. It appears as a groove or crater near the outer edges of the weld and is often the result of welding with too high of voltage or using an incorrect weld angle.
Wagon Tracks – Also called worm tracking, these are weld defects caused by hydrogen that has been trapped by the freezing slag. They appear when a bubble flows into the weld puddle and evaporates into the atmosphere, and are typically caused by excessive voltage.
Getting it right about equipment
You can’t get the job done without the proper equipment. And even though most of the focus is on the power source, other components play an important part in the SMAW process, too, including these.
Stinger – Another name for the SMAW electrode holder, it comes in various sizes for light- to heavy-weight welding applications.
Whip – Refers to the cable connected to the SMAW electrode holder or stinger. This cable is typically 10 to 15 feet long.
Don’t get stuck on SMAW electrodes
SMAW electrodes come in a variety of diameters and alloys to meet the needs of differing base materials and industry applications. Each has its own unique arc and burn-off characteristics, as described here.
Rods – An informal term for a SMAW electrode.
Cellulosic – Refers to SMAW electrodes featuring organic material, including paper, as the main component. These electrodes tend to have deep penetrating capabilities.
Low Hydrogen – Refers to SMAW electrodes that provide weld deposits containing a low amount of hydrogen gas, typically 4 to 8 ml per 100g of weldment. The low amounts of hydrogen help minimize cracking in the completed weld.
Fingernail – This term refers to the shape of the SMAW electrode as the flux burns off the end.
Unloading – The way a SMAW electrode, typically an AWS 7018 classification, burns off while welding. It occurs as a large amount of the SMAW electrode releases across the arc, often resulting in additional spatter.
Keeping up with SMAW lingo isn’t critical to achieving good welds. That’s, of course, a matter of following proper procedures, practice and careful attention to technique. However, knowing some of the common terms used to refer to
different aspects of the process may help you communicate effectively with others and avoid confusion on the job.